髪の毛1本に5000本の線!
スタンプで描く半導体の未来
次世代の半導体微細加工技術「ナノインプリントリソグラフィ」開発秘話
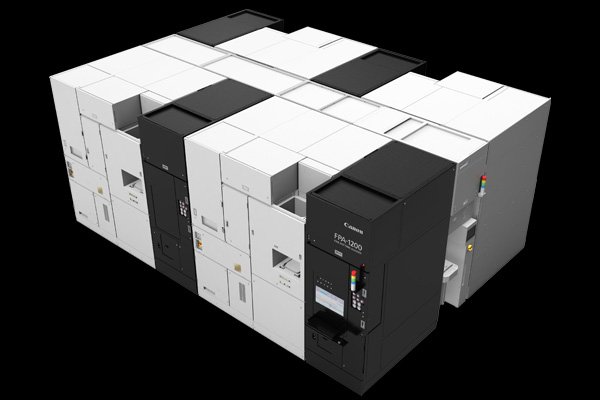
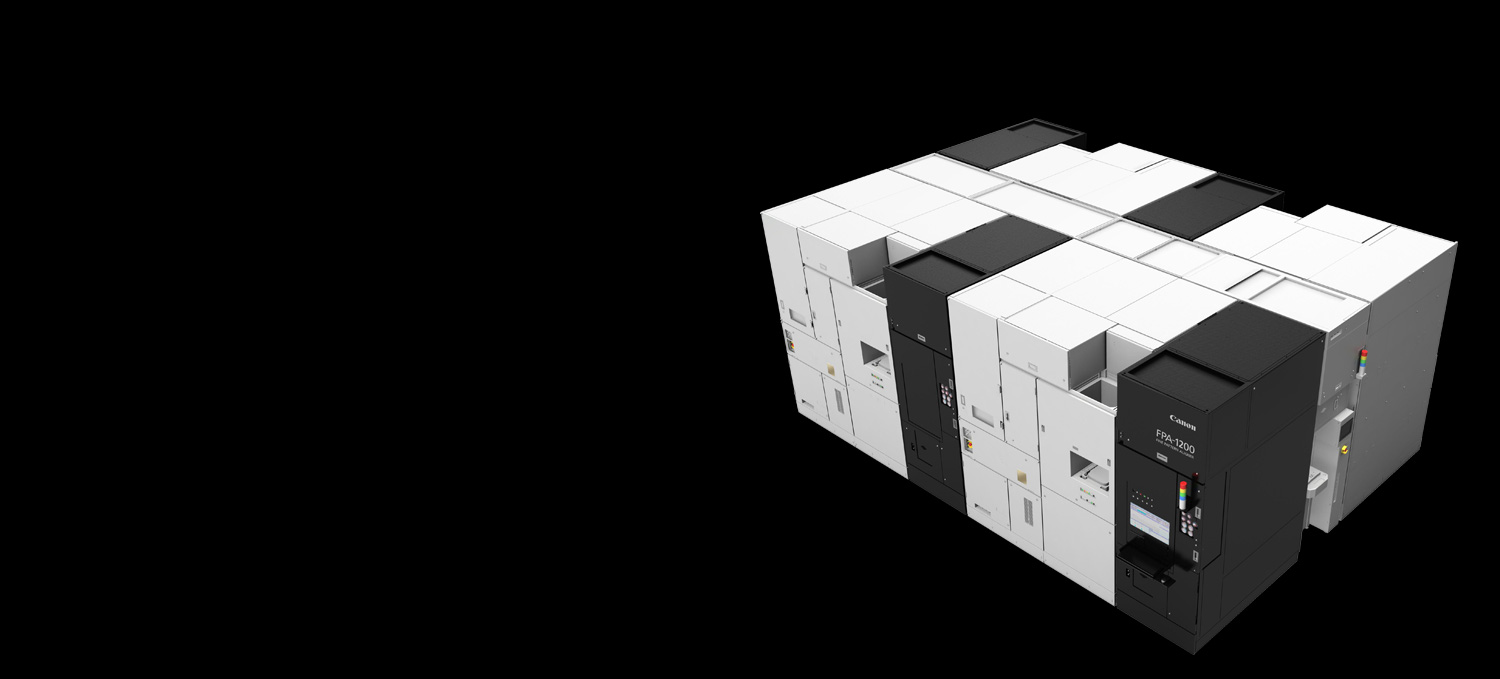
イントロダクション
半導体製造装置の常識が、
刷新される瞬間がまもなくやってくる。
半導体は現代社会になくてはならない存在だ。半導体とは、ウエハー(基板)上に微細な電気回路を描いて機能をもたせたもので、主な用途としては、メモリー(記憶)、ロジック(計算)、センサー(認識)などがある。スマートフォンやパソコンをはじめ、家電製品や自動車など身の回りのあらゆるところに使われており、IoTや、さまざまな分野で注目されるAIの発展にも欠かせない。
今はスマホや携帯電話で動画を撮影し保存できるのが当たり前となっているが、かつては静止画も扱えず、保存できるのは文字データだけだった。文字から静止画、静止画から動画へと、大きなサイズのデータが扱えるのは、半導体チップの劇的な進化によるものである。ウエハー上の同じ面積にたくさんの回路を描き、記録できる情報量を増やすためには、回路の線幅を細くしていく必要がある。半導体の世界では、これを「微細化」と呼ぶ。
これまでその微細化は飛躍的に進化してきたが、近年、物理的な限界が見えてきた。そのような中で現れたのが、ナノ*レベルでマスク(型)を押し付け(インプリント)、回路パターンをつくるという「ナノインプリント」である。限界が見えてきた従来方式とは一線を画す、全く異なる技術で微細化を実現できる次世代製造技術として、キヤノンが世界で初めて量産装置を開発。すでにこの装置「FPA-1200NZ2C」は半導体メモリーのリーディングカンパニーである東芝メモリに納入されている。
このナノインプリントリソグラフィには、一体どんな技術が使われているのか、従来の方式とは何が異なるのか、そして私たちの暮らしに何をもたらすのか、開発担当者に聞いた。
* 1nm(ナノメートル):10億分の1メートル
今回の「語る」開発者
-
首藤 伸一シュドウ シンイチ
担当:機械設計 -
中山 貴博ナカヤマ タカヒロ
担当:要素開発 -
小笠原 昌輝オガサワラ マサキ
担当:電気設計 -
日下 敦之クサカ アツシ
担当:プロセス開発
01
新技術紹介 非接触から接触へ。
劇的な転写プロセスの変更は、
一度は開発担当者に「できない」と思わせた。
read more
-
- 首藤 伸一シュドウ シンイチ
機械設計担当。入社以来、半導体製造装置の機械設計一筋。
モットー:悩んだら一歩前に出てみる
「やるかやらないかで迷ったら、やってみようという気持ちで取り組んでいます。」
ナノインプリントの話をお聞きする前に、まずは従来の半導体製造装置の役割について教えて下さい。
日下 敦之通常、半導体チップは、半導体のシリコンを薄い円盤状にスライスしたウエハーに、成膜、露光、現像、イオン注入などを繰り返して生産されます。その中でキヤノンが開発・製造する半導体製造装置は、実際に回路パターンを焼き付ける露光の役割を担っていて、半導体チップの微細化と生産性に最も影響する重要な工程の一つです。
半導体チップの製造工程
-
レチクル(原版)を作成
半導体チップの機能や性能を決める電子回路を設計。回路パターンは、何十枚ものガラス板に描かれる。
-
ウエハーを用意
半導体チップのもととなる円盤状のウエハーを用意。加熱して表面に酸化膜をつくった上に、レジスト(感光剤)を塗る。
レチクルに光を当て、回路パターンをウエハーに露光する。光をレンズで縮小することで、より細かい線を描くことができる。回路の線幅を細くすればするほど、一つの半導体チップの中に入る半導体素子が増えて、高性能・高機能な半導体チップができる。
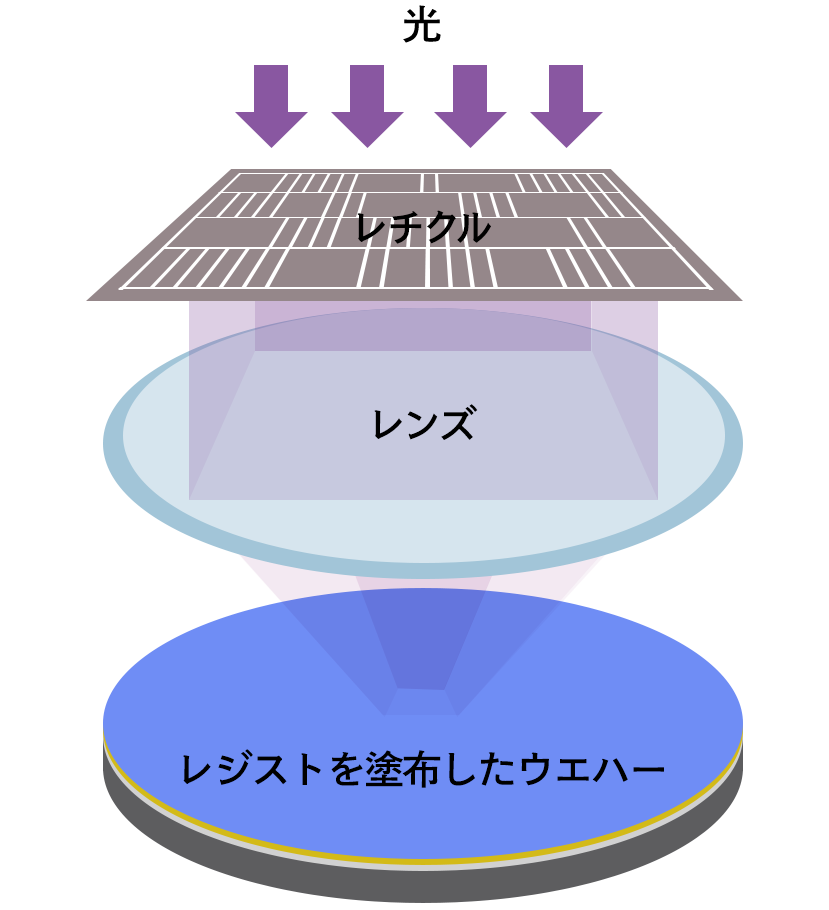
回路の線幅を細くすればするほど、一つの半導体チップの中に入る半導体素子が増えて、高性能・高機能な半導体チップができる。
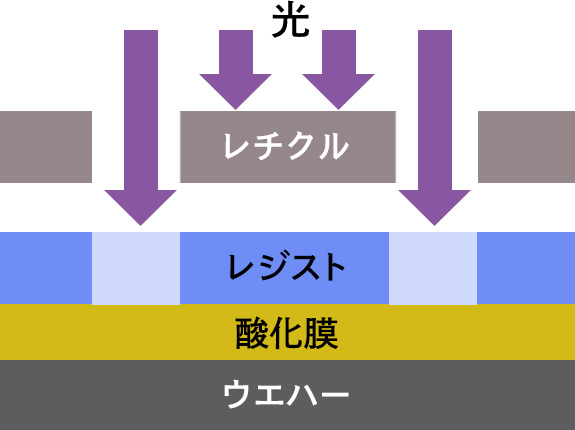
光が当たった部分のレジストが変化。現像液を使い、感光した部分を取り除く。
レジストで覆われている部分以外の酸化膜は、ガスと反応して除去される。
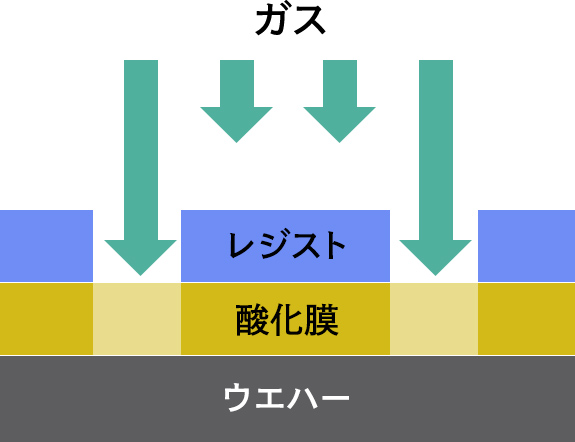
不要なレジストを除去後、露出したウエハー内に、トランジスタを効率良く動作させるための不純物を注入して半導体素子をつくる。

ウエハー全体を絶縁膜で覆った後、凹凸がないよう表面を平らにする。さらに次の層を重ね、回路パターンの露光に備え、レジストを塗る。
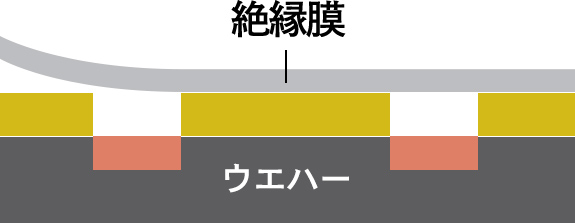
-
①から④を繰り返して回路の層を形成
工程を繰り返し、ウエハー表面にいくつもの層を形成。多層化して配線でつなぐ。
-
チップの切り出し
ウエハーから半導体チップを切り出す。
-
組立・完成
チップをフレームに貼り付け、ワイヤーで結ぶ。検査工程を経て完成。
ナノインプリント方式を用いた半導体製造装置の開発は、どのように進められてきたのでしょうか。
中山 貴博キヤノンが開発に着手したのは2004年です。当時から微細化の停滞問題は業界内外で話題となっていて、従来型の半導体製造装置に替わるものが求められていました。装置メーカー各社では、露光の光源に波長13.5ナノメートルという極端紫外線を用いるEUV(Extreme Ultraviolet)方式、回路パターンを電子線で描くEB(Electron Beam)方式などが検討されていました。しかし、複雑な機構で非常に高額な装置になってしまったり、生産性の向上が困難であるなど、多くの問題を抱えていました。
そこでキヤノンはいち早く、シンプルでコンパクト、低コストでチップがつくれるというメリットをもつナノインプリント方式に絞り込みました。社内に小規模のナノインプリント開発部隊が誕生し、最初は社内でも極秘のプロジェクトでした。そして2014年、ナノインプリントの基本技術の開発を手がけてきた米国のモレキュラーインプリント社(現 キヤノンナノテクノロジーズ社)がキヤノングループに加わったことが公になり、社内にも、そして世の中にも、キヤノンはナノインプリント方式で開発を進めていくということが明らかになりました。
首藤 伸一私は開発部隊に途中から加わったのですが、実際に手がけると知ったときには、正直言うと「そこまで精密なものが本当にできるのか?」と思いました。
そのように思った理由として、従来方式の装置との違いや難しさを教えて下さい。
首藤 伸一これまでの装置は光を使って回路パターンを転写するのですが、ナノインプリント方式の特徴は、回路パターンをハンコのようにスタンプするところにあります。液滴状にしたレジスト(樹脂)を、ウエハー上に「塗布」し、マスクをそのレジストに押し付ける「押印」とそれの「重ね合わせ」、そしてマスクをレジストから引き離す「離型」という工程を経てパターンがつくられます。非接触で行ってきたプロセスを接触させて行う点が、従来と最も大きく異なる特徴です。
ナノインプリント方式の特徴
-
01
インクジェット技術を使って、液滴状にしたレジストと呼ばれる樹脂を回路パターンに合わせてウエハー上に塗布
-
02
回路パターンが彫り込まれたマスクと呼ばれる型をウエハー上に塗布されたレジストにスタンプのように直接押し付ける
-
03
紫外線でレジストを硬化させて回路パターンをつくり、マスクをレジストから引き離す
中山 貴博マスクをスタンプするメリットは、高解像度できれいな回路パターンを描けることです。
また、ナノインプリント方式では、光露光装置に使われている光源や大口径のレンズ群が不要なため、装置自体をシンプルかつ安く、コンパクトにすることができます。装置が小さいので、複数台のナノインプリント装置を並べて、生産性を高めることも可能です。
小笠原 昌輝ナノインプリント方式では、ナノ単位のパターンをつくります。よく人間の髪の毛の太さは、直径が約100ミクロンと言われますが、そこに幅20ナノメートル間隔でパターンを描画しようとすると、5000本もの線を引けることになります。みなさんが想像するハンコのイメージとは別次元の細いパターンをハンコでつくろうというのがこの試みです。
日下 敦之従来の装置で用いられるマスクは、実際の回路パターンの4倍の大きさで、それをレンズで縮小してウエハーに焼き付けるのですが、今回のマスクは直接押し付けるので等倍です。単純に求められる精度は4倍まで高くなりますし、先ほど髪の毛の例があったように、非常に微細にもなります。さらには、その小さなマスクとウエハーとの位置合わせもでも、高い精度が求められることになります。
そのような難しさがあるにもかかわらず、ナノインプリント方式に挑んだのは、どのような理由からですか。
小笠原 昌輝従来の装置に替わる可能性がある方式の中で、お客さまからのニーズに最も応えられそうなのが、ナノインプリント方式だったからです。ほかにも、微細なプロセスが可能な方式はあります。しかし、その装置には莫大なコストが必要となると、その半導体チップを搭載するスマホやパソコンといった商品が高額になってしまいます。キヤノンがナノインプリント方式の装置を開発すれば、より安く、多くの方にさまざまな商品やサービスを使ってもらえると思っていました。また、この開発に着手した当初、キヤノンは半導体製造装置業界では他社に差をつけられ、苦しい立場にいました。このナノインプリント方式をいち早く実用化に結びつけることで、業界のナンバーワンになりたいという思いもありました。
02
開発物語 進めば進むほど出てくる課題を
一つひとつ解決していくほかに、
精度を上げていく方法はなかった。
read more
-
- 中山 貴博ナカヤマ タカヒロ
要素開発担当。各担当者と連携し、パーティクル抑制などの課題解決に取り組んできた。
モットー:あしたはあしたの風が吹く
「追い込まれた時などにふと思い出すと、まぁなんとかなるかと、前向きな気持ちになります。」
実際に開発を進める中で、課題はどのように解決したのですか。まず、レジストの塗布について教えて下さい。
首藤 伸一従来の装置では、ウエハーの表面に均一にレジストの膜を形成します。
しかし、ナノインプリントの場合は、必要なところだけピンポイントで、レジストを液滴状に配置します。その制御は簡単ではありませんでしたが、飛翔する液滴の量や状態を測定し、制御する部分には、キヤノンがプリンターで培ったインクジェットの技術を活用することができました。
押印についてはいかがですか。
小笠原 昌輝押印では、ウエハーとマスクの間に入る空気が問題になります。スマホの画面に保護フィルムを貼るのをイメージするとわかりやすいと思いますが、なかなかきれいには貼れませんよね。ナノインプリント方式の押印でも、ウエハーとマスクの間に空気が入ると、パターンを正確につくることができません。
中山 貴博マスクは厚くて硬いのですが、そのマスクの中心部分だけを周りよりも薄くし、マスクを少しだけたわませることにしました。すると、まずウエハーとマスクの中心部分が密着し、そこから放射状に密着する面積を増やしていけます。そうして、空気が外へと逃げていくようにしたのです。
また、どんな状態のウエハーにも、狙い通りの位置に押印をしなくてはなりません。ウエハーはどれも同じに見えても、製造工程の違いなどによってナノレベルでは大きな個体差があります。そういった差のあるウエハー一枚一枚に、一つのマスクで全く同じパターンを形成し続けることが難しいことも開発の過程でわかってきました。しかし、お客さまにとって「従来の製造装置ならできたことが、ナノインプリント方式ではできない」では困ります。そこで、押印の瞬間にだけウエハーを部分的に加熱し、マスクに合うようにナノレベルで変形させることで、マスクとぴたりと合うようにしたのです。熱は変形の原因であり、抑制すべきものだというのが、これまでの半導体製造装置の常識だったので、固定概念が覆りました。
ズレのない重ね合わせに欠かせない、位置やサイズの調整に関してはいかがですか。
日下 敦之半導体デバイスはさまざまな装置を使用し、複数の工程を経て製造されます。
前の工程で形成されている回路パターンの上から新たなパターンを描画し、厚み方向に数十層のパターンが形成されて製品となるため、下層の回路パターンとの位置関係が精密に合っていないとデバイスとしての性能が得られません。しかも、下層の回路パターンは必ずしも理想的な形状ではなく、製造の過程でさまざまな形状に変形していて、どのような形状であったとしても柔軟に対応する必要があります。これを重ね合わせと呼び、装置の重要な性能指標の一つとなっています。
最初にすることはパターン全体の大きさや形状の調整ですが、それでも精度を高められなければ原因を探します。装置が駆動すると温度が変わり、温度が変わるとマスクやウエハーは膨張・収縮してサイズが変わります。設計時には当然、それを見込んでいるのですが、想定と違う結果が出た場合は、ズレ度合いを計測する点数を増やし、得たデータをチェックし、では次はこの条件を変えてみようという具合にフィードバックを繰り返します。そうして、ベストの条件を探し出していきます。
小笠原 昌輝サイズ合わせがうまくいかない原因は、設定温度と実際の温度が違っているからではないかという話になったこともありました。
温度に関しては0.02度という極めて微少な差の範囲に抑えなければいけません。
周りから「本当に言ったとおりの温度になっているの」と言われたのは覚えています。でも、そこで「なっています」と答えて終わりにするわけにはいかないので、あえて温度を変えたり、測るポイントを変えたりしながら、「原因はこれじゃないね」「あれじゃないね」と切り分けていきました。
日下 敦之重ね合わせの位置の調整については、マスクとウエハーに特殊なマークを描画することで、位置関係を計測しています。
レジストには粘性があるため、接触によって力が働き変形します。この変形は樹脂の種類や状態によっても微妙に変わるため、これらを精度よく補正するには高度な技術が必要です。
次は離型について教えて下さい。
小笠原 昌輝マスクを離すときは、水平な状態を保ったまま一気に離すのが良いと思っていましたが、そうするとウエハーからマスクを引き離す際に非常に大きな力がかかってしまうので、ダメージを与えないように引き離す方法を考えなくてはなりませんでした。では、ノートをめくるように端の方から徐々に剥がせばいいかというと、斜め方向に引き離すことによってウエハー上にせっかくつくったパターンが、マスクによってなぎ倒されてしまう可能性が出てきます。
ナノインプリントリソグラフィ(03分39秒)
小笠原 昌輝ここでも、これまで考えていた常識が覆りました。あえてウエハーを部分的に持ち上げることで傾け、ウエハーとマスクが一対の歯車のように動くようにしたことで、パターンをきれいに保ったまま離すことができるようになったのです。私たちの常識では、ウエハーは持ち上げてはならないものでしたので、まさに逆転の発想でした。
さらに、マスクを破壊しないために気をつけているのは、パーティクルの除去です。
パーティクルとはどのようなものでしょうか。
首藤 伸一先ほど押印のところで、空気が入るとパターンを正確につくることができないという話がありましたが、同じように厄介なのが、パーティクルです。
パーティクルとはゴミのことで、ウエハー上にマスクを接触させてパターンを描画するため、パーティクルが間に挟まると、マスクのパターンを破壊してしまう可能性があります。
中山 貴博少なくとも、直径が数十ナノメートルサイズのパーティクルはゼロといったように、従来の装置よりも厳しい仕様が求められます。そこまでになると、その目標値を評価する測定器自体が存在しないので、今は「世の中にある最も感度の高い測定器で検出できる下限値より下」が実質的なゴールになっています 。
超高性能フィルターとクリーン化技術による「パーティクル抑制」(34秒)
首藤 伸一見えないけれど、そこに確実にある何かをなくそうとする作業なので、そう簡単ではありません。
中山 貴博まず、そのパーティクルがどこから発生しているのかを突き止めるところから始めます。どこからなのか、その発生元がわかると、取り除くことができるかどうか、機械設計の担当者と検討します。そうして一つひとつの可能性を泥臭く減らしていくのです。
首藤 伸一例えば、パーティクルを抑制するために空調の機構を追加しようとすると、限られた空間に、そのためのスペースを確保しなくてはなりません。すると、ほかの機構を移動させたり、配管の配置もやり直したりする必要も出てきます。そうしてパーティクルが減ればいいのですが、うまくいかない場合は検討からやり直しです。何度も図面を描き直す必要が出てきます。
中山 貴博それを毎回、実際に組み付けてくれるのは工場の方です。手間が増えてしまうのですが、何に困っていてどうしたいのかを伝え、協力してもらい、より良い状態を得られるようにしてきました。
また、外注先ともこれまで以上に密にコミュニケーションをとりながら進めました。まだやったことのない領域の仕事なので、材料の選定や加工の方法など、思わぬところでパーティクルの発生に大きな影響を与えるようなこともあるからです。外注先はさらに外注先に委託していることが多いのですが、その二次外注先とも材料リストやマニュアルを共有するようにしてきました。
地道な作業の積み重ねなのですね。
首藤 伸一パーティクルに関しても、1/100、1/1000という単位で減少してきましたが、劇的なブレークスルー技術だけでは解決できない部分がたくさんありました。
中山 貴博精度を上げるには、まずはシミュレーションをして、その通りかどうか実際に検証するという泥臭い作業の繰り返しです。ただ、シミュレーションには「こうしたらよくなるのでは」というアイデアが欠かせないので、そこで先ほども話にあがったような、逆転の発想やそれまでにないアイデアが出てくるかどうかは大きいと思います。
新しい課題が見つかったら、まずは自分たちのチームで何とかできないかを考えるのですが、同時に関係者に共有し、みんなで解決していくというループがいくつもできていました。なので、みんなでやっているという実感は常にありましたね。めざすところは毎日のように高くなっていくのですが、走りながらフィードバックして前に進めていくことができたと思っています。
今回の開発では、米国のキヤノンナノテクノロジーズ(以下 CNT)と協業しています。どのような連携がなされたのでしょうか。
CNTからの出張者との打ち合わせ
小笠原 昌輝CNTはナノインプリント方式に関する基本技術を開発し、それをキヤノンが量産装置に展開するという役割分担のもとで、協業を進めてきました。CNTはスピード感があり、発想も柔軟で、常識にとらわれがちな自分たちの頭の固さを痛感させられたことが、何度もありました。
首藤 伸一CNTのような意思決定の速い会社と仕事をすることで、刺激になりました。今回の協業は、M&Aも行いながらグループ会社と連携して新規事業に注力している、キヤノンのモデルケースになり得ると思っていて、個人的にはそこにも面白さを感じています。
03
新技術への挑戦を通じて得たもの チャレンジは開発者の心に火をつけ、
協業の可能性を切り拓いた。
read more
-
- 小笠原 昌輝オガサワラ マサキ
電気設計担当。入社以来、半導体製造装置開発でキャリアを積んできた。
モットー:顔を合わせて話をする
「大きな装置なので、さまざまな場面でさまざまな立場の人が協力することが必要不可欠です。顔を合わせて話をすることは、そのための最も効果的な手段だと思っています。」
-
- 日下 敦之クサカ アツシ
プロセス開発担当。性能評価担当を経て、重ね合わせの精度向上に努めてきた。
モットー:自分の言葉で説明できるようにする
「理解できていることは、自分の言葉で説明できると思います。少しずつでもいいので、自分が理解できる領域を広げていきたいです。」
世界初の装置です。開発を進める中で、新たに直面した課題もあるのではないでしょうか。
小笠原 昌輝新しい方式なので、開発していくうちにわかることもありますが、わからないことも同様に増えて、ナノインプリント技術の奥深さを実感していきました。
日下 敦之あまりに微細すぎて、自分たちの知っている物理現象では説明できないことや、これまでの方法では実際に起きていることがシミュレーションできないケースも増えています。プロセスの担当としては、しっかりメカニズムを解決してやっていきたいと思っています。
新方式を開発したから新たに発見されるものもあるのですね。
首藤 伸一過去の蓄積を生かすだけでは、ここまで来られなかったと思います。ナノインプリント技術は、従来の製造装置と比較すると、排気にしても温度にしても当初の想定以上に要求精度が厳しく、新たな技術開発が必要でした。また、さまざまな想定外が発生し、何度も再設計が必要になり苦労しました。実際には難しいのですが、品質だけでなく、コストやスペースなどあらゆる観点で余裕をもった設計を常に意識することが重要だと、日々感じています。
中山 貴博この開発に携わったことで、新しい領域に挑戦しようとすることは、その領域の測定装置やシミュレーションといったインフラを整えることでもあるのだと知りました。何もないところからの挑戦は苦しくもありますが、自分たちの成長の糧にもなると思っています。
今回、ナノインプリント方式の半導体製造装置の開発に関わったことを、ご自身のエンジニアとしてのキャリアの中でどう位置づけられますか。
首藤 伸一これまでの常識を覆す、ここまで大きなプロジェクトに関わるチャンスは、なかなかないと思います。技術者としてはそこに最大の喜び、楽しさを感じています。
小笠原 昌輝最先端への挑戦ですし、お客さまから期待もしていただいていて、やりがいはもちろん感じています。個人的には、以前設計に関わっていた装置がうまくいかなかったという経験もしているので、今回はなんとしても成功させたいと思っています。
日下 敦之従来、ウエハーを露光した際の課題は製造装置メーカーであるキヤノン単独の問題であることが多かったのですが、ナノインプリントは接触方式であるため、製造装置以外のさまざまな影響を強く受けるようになりました。
CNTをはじめとした企業と協業して解決できた問題も多くあり、他社との協業の必要性を強く感じるとともに、新しい発見が多く刺激の多い毎日です。
また、私自身は今回、米国テキサス州のオースティンにあるCNTへの長期出張も経験しました。ベンチャー企業特有の意思決定のスピードの速さや、契約社会であるため、業務分担が極めて明確であること、また各自が成果の出し方、見せ方を常に工夫している点など数多くの新たな発見があり、人生観が変わるほど、そこでの経験は大きな財産になっています。
首藤 伸一私は半導体業界に元気がなかったリーマンショック前後の時代も経験しているので、今この業界が盛り上がっていること、その最先端でチャレンジできていることをうれしく思っています。
装置はすでに2017年7月に東芝メモリ四日市工場へ納入されています。 今、どのようなお気持ちですか。
東芝メモリ四日市工場で調整が進むナノインプリント半導体製造装置「FPA-1200NZ2C」
日下 敦之「やっとだな」という思いもあります。ただ、ここからが本当の勝負だと思っています。半導体製造装置は納入されたら終わりではなく、お客さまの要望を満たすため、納入後にさまざまな調整が必要な製品です。お客さまから要求されている内容を正確に把握し、いろいろな人の協力を得ながら素早く対応することで、お客さまに認めていただける装置にしていかなくてはと思っています。ただ、このレベルまでくると、装置の性能は何か一つを変えれば劇的に上がるわけでありません。こうすれば良くなるであろうと信じていることを少しずつ進めて、高めていくしかないのです。
小笠原 昌輝私も、ここからが本番という思いの方が強いですね。市場から大きく期待されていると強く感じますので、期待にも応えたいですし、市場で使われるようになった後も装置を改良するため、今後も努力を続けなくてはなりません。
半導体は現代社会を支える存在です。その製造装置の次世代のスタンダードに関わっていることをどのように感じていますか。
中山 貴博この2、3年が勝負、という思いもある一方で、この先のことは非常に楽しみでもあります。私は研究部門にいたことがあり、その当時はなかなか製品を世に出す機会がありませんでした。しかし、ここでこの装置に関わったことで、早ければ今年中にもフィードバックが得られそうです。現在、半導体デバイス向けのナノインプリント装置を製造している企業はキヤノンしかないこともあり、大きなやりがいを感じていますし、しっかりと社会に貢献していければと思っています。
首藤 伸一ナノインプリント方式のこの装置は、未来をつくる装置だという気概を私はもっています。これからの半導体はより微細化し、スマホの中に詰め込まれるだけでなく、将来はシールのように人の皮膚に貼り付けたり、コンタクトレンズの中に仕込んだりという使い方がされていくでしょう。それをお客さまの求めるコストとスピードで実現できるのは、ナノインプリント方式だけだと思っています。
また、IoTやAIにも半導体は欠かせません。従来、大容量の記憶装置にはハードディスクが多く使われていました。現在、クラウドサービスで用いられる大容量のデータを保存するデータセンターでは、小型大容量で、高速かつ低消費電力という長所をもつ半導体メモリーが必須の技術となっています。半導体はそれだけ期待されている存在であり、その製造を支える私たちの仕事は、これからのより快適で便利な社会を支えていく仕事でもあると感じています。
エンディング
これまでの常識を捨てる覚悟と、アイデアを製造装置に展開するための地道な努力。この2つがあったからこそ、さまざまな苦労を乗り越えて、世界で初めてナノインプリントの量産装置を開発することができた。いずれ、半導体を利用したIoTやAIは私たちの暮らしに当たり前のように溶け込み、今よりも格段に便利で快適な社会を支えているだろう。ナノインプリントもその社会の実現に貢献しているに違いない。
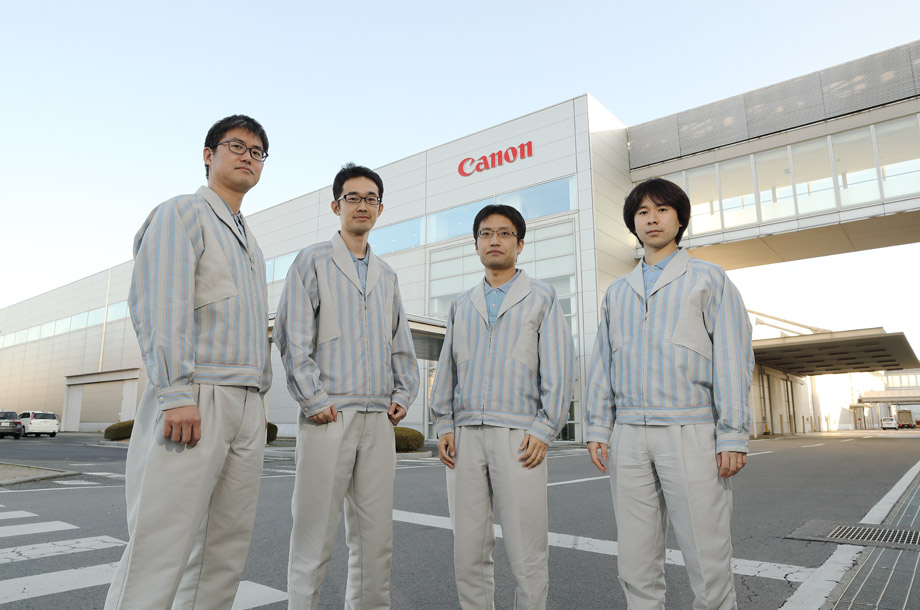
インタビューを終えて
「世界初」という言葉につきまといがちな興奮した様子がなく至って冷静な口調で語ってくれた。
話を聞いているうちに、その理由に気付かされた。問題があればそれを解決するのは、彼らにとって当たり前のことなのだ。産業の発展とその先にある人々の豊かな暮らしをめざし、顧客からの高い期待に正面から応えようとする姿勢は、キヤノンの企業理念「共生」と、創業期から受け継がれる行動指針「自発・自治・自覚」の「三自の精神」と通底している。
インタビュー・構成 : 片瀬 京子 1972年生まれ、東京都出身。1998年に大学院を修了し、出版社に入社。雑誌編集部で記者、編集者として働き、2008年から、フリーランスのライターとして活動。共著書に『ラジオ福島の300日』など。