「見たまま」の世界を再現!
撮りたい想いに応えるレンズをつくる
非球面レンズ/DOレンズ/BR光学素子/SWC・ASC「高性能レンズを生み出す生産技術」開発秘話
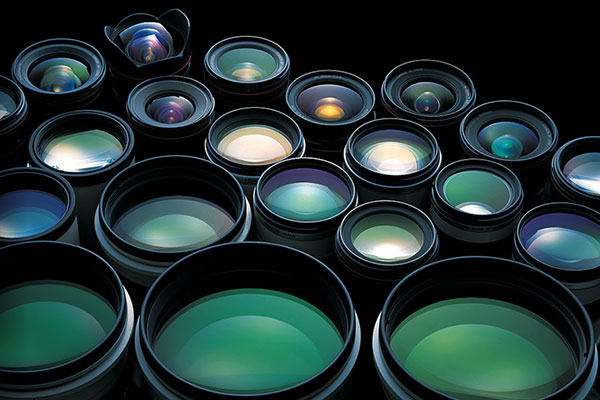
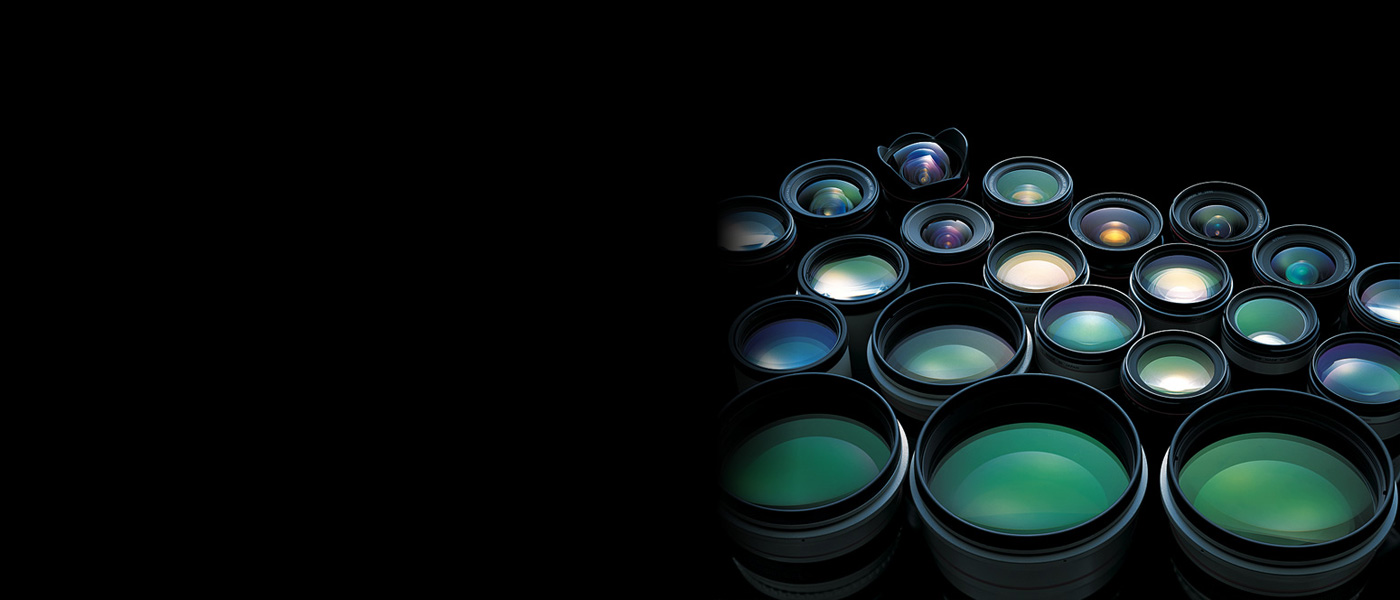
イントロダクション
光の性質を利用し物体の「像」を再現することによって、さまざまな情報を伝える、カメラ、プロジェクター、オフィス向け複合機、プリンター、医療機器などの光学機器。搭載されている光学技術は、私たちの暮らしを根幹から支えるテクノロジーのひとつだ。
キヤノンの光学技術は、材料から設計、加工までさまざまな技術が結集し、高精度な機器や、新しい性能を持つ機器をつくり出してきた。世の中にはまだ存在していない新しい材料を開発し、「理論上は可能」とされてきた現象を実際に形にするなど、求める性能を実現し、多くの人に届けるためには、生産技術が欠かせない。
その中で、世界最先端の技術であるカメラレンズの生産技術に今回は焦点をあてる。
最先端の技術にはどのようなものがあり、それはどのように生まれ、どこに向かっているのか、開発担当者に聞いた。
- 詳しく知りたい
- レンズの仕組み(1分14秒)
今回の「語る」開発者
-
中川 英則ナカガワ ヒデノリ
担当:研磨 -
宮沢 俊一ミヤザワ シュンイチ
担当:ガラスモールド加工 -
丹羽 麻衣子ニワ マイコ
担当:DOレンズ加工 -
齋藤 輝伸サイトウ テルノブ
担当:BR光学素子 -
槇野 憲治マキノ ケンジ
担当:高性能反射防止膜
01
非球面レンズ収差を補正し、忠実な像再現を可能に。
研磨とガラスモールド、2つの工法がめざしたものとは。
read more
非球面レンズ(3分4秒)
-
- 中川 英則ナカガワ ヒデノリ
加工プロセス開発担当。非球面レンズや自由曲面ミラーなどの研磨技術の開発に従事してきた。
モットー:いま気づく
「問題の原因や解決の糸口が何かを気づくために今ここに自分がいる、という気持ちで加工の現場に向き合っています。」
「非球面レンズ」とはどのようなレンズですか。従来の球面レンズと比べてどのような違いがあるのでしょうか。
中川 英則球面レンズには、「平行光線を完全な形で1点に収束させられない」という宿命ともいえる課題があります。レンズの面が球面であるために、レンズの縁を通る光がレンズ中心部を通る光よりもレンズの中心近くに集まってしまい、その結果、像が少しぼけてしまう「球面収差」が出てしまいます。この球面収差を補正するには、何枚ものレンズを組み合わせなければなりません。そこで、1枚で球面収差をなくすレンズとして開発されたのが非球面レンズです。
非球面レンズは、文字通り、レンズの面が 「球面」ではありません。曲率を径方向に微妙に変え、断面を見るとレンズのふちに少しくぼみのあるような形になっています。この形状にすることでレンズを通過する光は1点に集まり、ぼけのない忠実な像が得られます。
球面レンズと非球面レンズの違い
非球面レンズを作る技術としては、どのようなものがありますか。
中川非球面レンズの作り方は主に4種類あり、削って磨く「研磨法」、金型でガラスを成形する「ガラスモールド法」、ガラスとプラスチックを組み合わせた「レプリカ法」、金型でプラスチックを成形する「プラスチックモールド法」があります。ガラスの非球面レンズでは、研磨法とガラスモールド法の2つがあります。
非球面レンズの研削方法
研磨による球面レンズ加工の考え方は、工具の形をそのまま転写するというものです。作りたいレンズの形と反転形状の工具を、レンズ材料と擦り合わせることによって工具の形を転写します。
一方、非球面レンズは、レンズの面が複雑な曲線を描くため、お互いを擦り合わせるという方法では作ることができません。
研磨での非球面レンズは、ダイヤモンドの入った工具である砥石が回転しながらレンズを削り、非球面の複雑な形状を作るように動きます。レンズと砥石の削る位置を制御する加工機の精度がそのままレンズの精度に影響するので、非常に高い精度の加工機が求められます。
-
非球面レンズの研削
キヤノンが非球面レンズを最初に開発したのは1970年代初めでしたが、量産化までにはどのような課題を克服する必要があったのですか。
中川まず、レンズを設計した通りの非球面の形状にするために、100ナノメートルレベルの位置決め精度で動くことのできる加工機が必要だったことです。加工原理は確立されていても、それに装置が対応できなかった時期が長かったのです。1960年代後半、コンピューターで動きを制御するNC工作機械が出始め、1970年代にそれを取り入れることで非球面レンズが量産できるようになりました。それから約半世紀を経て、今では当時の100倍以上の精度が得られるようになっています。
研削機の動きは、回転しながら平行に動き、高精度に形を作るという複雑なものです。その後、さらに研磨の段階がありますね。非球面レンズの加工で最も難しいのは、どのようなところですか。
中川まずは、工具が高精度であることが必須です。研削段階ではダイヤモンドでバリバリ削っていくのでレンズは白くなります。研削でより透明度の高いレンズを得るためには、工具の形やダイヤモンドの状態などの管理が重要になります。研磨の工具は直径が大きいほど能率が高くなりますが、レンズより大きな工具を使うと球面レンズの研磨方法と同じになり、最終的に球面レンズになってしまいます。工具が小さいほど複雑な非球面形状に対応しやすいのですが、加工時間が長くかかってしまいます。時間と精度を両立するためには特殊な工具設計技術を用いないと非球面の研磨はできません。
そして、加工機の動かし方がポイントになります。加工機の精度任せだけではレンズの精度は達成できません。加工機、工具、加工機の動きを制御するソフトウエアの3つをどう組み合わせて所望のレンズ精度を得るかの工夫が最も難しいところです。意図した形状と加工後の形状の誤差について、原因が何かがわからないと3つの組み合わせを決められません。この原因の解明という課題に、工場、装置開発、プロセス開発のメンバーが真摯に長い時間をかけて取り組んできた結果が、非球面レンズの精度を成り立たせているのだと思います。
-
- 宮沢 俊一ミヤザワ シュンイチ
樹脂とガラスの成形プロセスを担当。
モットー:本質にたどり着くまで掘り下げる
「目の前のデータだけにとらわれず、広い視野で本質に近づけるよう取り組みたいと考えています。」
非球面レンズを金型で作るもう一つの工法、ガラスモールドについて伺います。どのような技術なのでしょうか。
宮沢 俊一精密な加工を施した非球面のモールドで、ガラスを直接プレスして作る工法です。もとになるガラスと、ガラスを変形させるためのモールドをセットして、加熱、プレスし、冷却した後、モールドから外して取り出します。
モールドを簡単に交換できることから、さまざまなレンズがガラスモールドで作られており、生産性に優れていることがメリットです。
-
非球面レンズのモールド
生産性を上げるポイントとしては。
非球面レンズのモールド
宮沢ガラスをプレスする際にかかるパラメータは、温度、時間、荷重の3つです。これらの設定を工夫し、加工プロセスにかかる時間を短くすることで、生産性を上げることができます。そのためには、高温にしてプレスするまでと冷却して取り出すまでを、いかに品質を保ちつつ速くするかがポイントになります。
どのような点が難しいのですか。
宮沢ガラスの種類は多くありますが、それぞれで成分が異なり、同じプロセスでガラスを加工することができません。また、形状ごとに加工する難しさの度合いが異なります。それぞれのガラスや形状に応じたプロセス設計をしていくことがガラスモールドの難しい点です。
ガラスモールドの技術はどんどん進んでいますが、まだわかっていないことも多くあります。その一つが、高温の中でプレスされるガラスがどのように押しつぶされていくのか、そして冷却されるときに何が起こるのかを数値化することの難しさです。
うまくいかなくてあれこれ試しているとき、上司から「ガラスの気持ちにまだなりきれていない」と言われ、最初は冗談半分かと思いましたが、自分なりに荷重を加えられたガラスはどう変形したいのだろうかなど、ガラス側の視点で考えることが大事だと気づきました。うまくいったときは、ガラスの気持ちが少しはわかったのかなと思えてうれしかったですね(笑)。
高精度の非球面レンズに関しては、凸面より凹面のほうが後に開発されたそうですが、技術的な難しさが違うのでしょうか。
宮沢レンズには、両面ともに凸だけ、凹だけの組み合わせのほか、片面ごとに凸と凹が組み合わさったものなどさまざまな種類があります。凸と凹ではモールドからの剥がれ方が異なります。そのため、形状に合わせた加工プロセスの開発が必要でした。
そういった形状による難しさは、設計段階である程度わかっていて予想もつくのですが、それを克服するための開発段階ではトライ&エラーの連続になりますね。
ユーザーとしては、ガラスモールドの技術が進むことで、さまざまな種類の高性能なレンズができると期待が膨らみます。今後の方向性はどうなっていくのでしょうか。
宮沢ガラスモールドは、あらゆる設計形状を成形できるわけではありません。今後はガラスモールドで加工できるガラス材料の種類と形状のバリエーションを増やし、ガラスモールドの領域をさらに広げていきたいと思います。
02
DOレンズギザギザの形状を持つ特殊な素子、DO。
全く新しい方法で色収差を補正する先進技術とは。
read more
DOレンズ(1分8秒)
-
- 丹羽 麻衣子ニワ マイコ
プロセス開発担当。DO製造工程の要素開発から量産工程確立までの検討を行った。
モットー:直感的に理解する
「全ては分からなくても、直感的に理解しようと心がけることで成長できることがあると思っています。」
「DOレンズ」とはどのようなレンズですか。
丹羽 麻衣子光は、レンズを通るとき屈折します。また、光が障害物に出会ったとき、障害物の裏側に回り込む性質があり、それを回折と言います。輪帯状に形成した「Diffractive Optics(回折光学素子)」という素子を使って光の屈折と回折の両方を利用し、色収差を補正するレンズがDOレンズです。
一般的な屈折レンズとDOレンズは、色収差が全く逆の形で発生します。凸レンズでは、屈折レンズは青→緑→赤の順に結像しますが、DOレンズは逆で赤→緑→青の順に結像します。この2つを組み合わせることで、色収差を互いに打ち消して補正させ、例えば望遠レンズを大幅に小型化・軽量化することができます。
DOレンズの原理(イメージ)
- 1 屈折レンズ
-
- 2 DOレンズ
-
- 1と2の組み合わせ
-
DOという特殊な素子がカギなのですね。
丹羽DOはレンズ表面に「のこぎりの歯」のようなギザギザの格子を作り、光を回折させて進路をコントロールします。DOを使ったレンズは屈折作用を活用するのではなく、複数の輪帯を通過した光が干渉する作用を活用した特殊なレンズになります。
このような形状のレンズは昔からあったのですか。
丹羽一つの色だけに対する素子であれば、CDやDVDなどの光ディスクに使われるピックアップレンズなど、いろいろな用途で使用されていましたが、可視光全域で回折作用を活用する光学素子は、キヤノンが初めて2001年に製品化しました。回折現象が屈折系とは逆の色収差補正効果を持つことは理論的にわかっていましたが、それを実際にカメラのレンズに組み込んだのは初めてのことでした。
DOレンズの種類と、それぞれの特徴を教えてください。
丹羽キヤノンが製品化したDOレンズには「積層型(2積層型、3積層型)」と「密着2層型」があります。
積層型には構造の違う2種類があり、2積層型は2枚のDOの間に空気の層がある形状に対し、3積層型は2枚あるDOのうち、1枚のDOを種類が異なる材料で覆っている形状になります。2積層型から3積層型へ開発が進むことにより、ズームレンズにもDOレンズを応用できるようになりました。
密着2層型の構造はもっと簡単で、密着した材料と材料の間にDOがあります。この構造のDOに「特殊樹脂材料」を使うことにより、可視光全域で高効率に光を回折させることが可能になりました。
DOレンズの構造
-
- 正面図
-
- 2積層型
-
- 3積層型
-
- 密着2層型
「特殊樹脂材料」とはどのようなものですか。
丹羽この材料を使うことで、回折によって曲がる光がほぼ100%になる理想的なレンズを実現することができます。このようなDOの性能を最大限に発揮させる材料をキヤノン独自に開発し、その材料を使って光学レンズを製造する技術を同時に開発することで、新規のDOを実現することができました。
特殊な材料の加工ですから、苦労も多かったのでしょうね。
丹羽一般的な材料なら簡単にできることがうまくいかず、特殊な樹脂をどう扱い、薄くするためにどういった作成方法にするかなど、技術的に難しい点がたくさんありました。
輪帯形状は、型の上に材料を広げ、紫外線を照射し硬化させて形成します。このプロセスでは、特殊な樹脂を設計通りの形状に成形することがポイントでした。理論的に答えは出ていても、実際にやってみると予想外の現象が起こることがあります。そこをどのように技術確立していくのかに苦労がありました。
でも、扱いが難しい分、やりがいも大きいと感じています。キヤノンは幅広い分野の技術を持っています。例えば材料ができても、加工技術がすごくても、どちらか片方だけではこうした特殊なレンズを作ることはできません。その両方があるのがキヤノンの強みだと思いますし、自分自身がその一端に貢献できたことをとてもうれしく思っています。
- 詳しく知りたい
- 回折の原理
-
- 障害物によって回折した光が、ある距離(ピッチ)で隣り合うと互いに干渉し強め合った光(回折光)が発生します。
-
- また、回折光はピッチの間隔や光の波長によって発生する角度が異なり、ピッチの間隔が狭いほど、光の波長が長いほど、回折光は入射光に対して大きな角度で発生します。これを利用しピッチの間隔を制御することで、1つの色の光が1か所に集光するレンズを作ることができます。
03
BR光学素子カギとなるのは青色の光。
それを制御する画期的な光学素子は、世の中にない材料を作ることから始まった。
read more
BRレンズ(1分13秒)
-
- 齋藤 輝伸サイトウ テルノブ
入社以来、光硬化性の有機材料の開発を担当。
モットー:とりあえずやってみる
「思いついたアイデアはできるだけ全部やり、新しい発見・経験を繰り返すことが次につながると考えています。」
「BR(Blue spectrum Refractive)光学素子」とはどのような素子ですか。
BRレンズの仕組み
齋藤 輝伸自然光は、それを構成する光の波長ごとに通常の光学レンズ素子における屈折率が異なります。そのため、通常のレンズでは1点に集光し像を結ぶことができません。こうした色収差を補正するレンズとして、これまでにもさまざまな光学素子が開発されてきましたが、短い波長域である青色を1点に集光することは特に困難でした。
その青色だけを大きく屈折させる性質を持つのがBR光学素子です。この素子を組み込んだBRレンズは、今までとは比べものにならないほど高い水準で色収差が補正でき、「点を点として表現する」ことが難しかった天体撮影でもにじみの極めて少ない高画質が実現できるようになりました。
-
BRレンズの仕組み
色収差の抑制イメージ
-
- 通常ガラス
凹凸レンズを組み合わせるだけでは、青色の波長を補正しきれず、集光位置のズレが色のにじみとなって現れる。 -
- BRレンズ
凹凸レンズに青色(短い波長域)の光を大きく屈折させるBR光学素子を採用すると、可視光の波長全域を1点に集光させることが可能。
材料そのものを自社開発されたとのことですが。
齋藤既存の技術を組み合わせたレンズ群だけでは補正できない色収差をどのように補正するか検討していたところ、設計部門から「青色を大きく曲げるという方法はどうか」との意見があり、そのような材料はないものかと探すところからスタートしました。
一般に流通している材料の中に、青色の光が大きく曲がる材料があるという知見は既にあったのですが、レンズ用の材料としては使用できない問題があり、求める性能を諦めざるを得ない部分がありました。それなら、すべてに妥協しなくてもよい独自の材料を一から開発しようということになったのです。
一から材料を作るというのは、とてつもなく長い道程に思えます。具体的にどのような作業をされたのでしょうか。
齋藤有機光学材料を分子設計から内製することは初めての試みであったため、まずは化学反応をさせられるような実験室を準備するところから始めました。
その後、材料シミュレーションと実際に合成して特性を評価することを繰り返しました。材料シミュレーションというのは、それが実際に合成できるものなのか、物質として安定しているものなのかなどは関係なく、数値を入れれば必ず結果が出るものです。ただし、特性のみを求めてシミュレーションを行うと、製造方法が思いつかないようなとんでもない分子構造が仕上がります。そのため、この分子構造ならこうすれば合成できるとか、この分子構造ならいろいろな条件下でも安定しているだろうということなどを考えて、実際に合成して評価するものを絞っていきました。
分子設計で行き詰まったときには、原料・試薬メーカーのカタログを1ページずつ眺めながら新しいアイデアをつくりだしていました。
光学特性ばかりが注目されがちですが、青色の光を曲げることだけではなく、材料自体の製造工程の問題や人体に対する安全性、材料を扱うときの作業性、長期間安定していることなど、材料として求められる条件を含めて「世の中にない性能」を求め、設計していくことが難しかったです。そういう意味では、かなりこだわりの詰まった材料になっていると思います。
困難を乗り越え完成したときは喜びも大きかったのでしょうね。
齋藤難しさの中に面白さがあるというか、地道な作業の積み重ねですが、やりがいや面白さはすごくある仕事です。探しているものを見つけて、それを使って性能が出たときは「やった!」と万歳したい気持ちでした。
そして、世の中で誰も作っていない、全く新しいものを作りあげたという達成感は今までにない大きいものでした。この仕事は個人に託された部分もかなりあるので、言われたことだけをやるのではなく「こういうことをやってみたい」という材料開発者のこだわりのところまでやらせてもらえることもやりがいにつながっています。
実際、「やってみないとわからない」ことが多いのが材料という分野です。私は「やってみたけれどダメだった」という結果を自ら体験しないと納得できない性格ですので、自分の手を動かして、目で見て確認するということを常に意識していました。
現在、BRレンズは「EF35mm F1.4L Ⅱ USM」に搭載されていて、カメラ誌の記事などで「これほど違うとは思わなかった」「本当にすごい」という評判を聞きます。旧型とは構造やレンズの数なども違うと思いますが、一番の違いはBR素子を使っていることにありますか。
齋藤その通りだと思います。他の部分ももちろん工夫しているのですが、色収差を補正する能力はBRレンズが効いているのだと思います。今後、搭載する製品を広げることも視野に入れ、さらなる高性能化に向けた研究と、コストダウンへの取り組みが始まっています。
04
SWC/ASC「くさび」と「空気化」で光の反射を劇的に抑制。
業界をリードするレンズコーティング技術に迫る。
read more
SWCとASC(1分50秒)
-
- 槇野 憲治マキノ ケンジ
材料開発担当。入社以来、高性能反射防止膜の開発に携わってきた。
モットー:現状に満足せず、常に上をめざす。
「技術の進歩に終わりはないという気持ちで新しい技術に挑戦し、良い写真を撮りたいと思っている方たちの気持ちに応えていきたいと考えています。」
まず、反射防止膜の役割と機能について教えてください。
槇野 憲治空気とガラスの境界面では屈折率が大きく異なるので、レンズ表面で光が反射し、レンズの光透過率は低下してしまいます。また、ゴースト(レンズ面で複数の反射を繰り返した光が、本来ないはずの画像として映った現象)や、フレア(逆光などの強い光がレンズや鏡筒で反射や散乱して、画面の一部が白っぽくなる現象)が起こります。こうした現象を抑えるため、レンズの表面に極めて薄い膜をコーティングし、反射を防いでいます。しかし、光の入射角などの条件によっては十分に抑制できないこともありました。
ゴーストとフレア
-
- ゴーストとフレアありの例
-
- ゴーストとフレアなしの例
SWCの構造
そこで、反射防止性能をさらに高めるため、ナノテクノロジーを使った最先端のレンズコーティング技術の開発に取り組むことになりました。
光の反射を防ぐには、外気と膜との境界面をいかに制御するかが重要です。2008年に製品への採用を開始した「SWC(Subwavelength Structure Coating)」は、レンズの表面に、可視光の波長(380~780nm*)より小さいナノメートル単位のくさび状の構造物を無数に並べることで、実質的に光が境界面を感じないようにするという画期的なコーティング技術です。従来、反射の抑制が難しかった斜めからの光にも優れた効果を発揮し、フレアやゴーストの発生を大幅に抑えることが可能です。
ただし、SWCのナノサイズの構造物を形成するには複雑な工程が必要になります。そこで、製法がシンプルで、かつSWCのような構造体を持たない、高性能反射防止膜を作ろうということから、「ASC(Air Sphere Coating)」の開発をスタートさせました。
* 1nm(ナノメートル):10億分の1メートル
-
SWCの構造
ASCはどのようなコーティング技術なのですか。
槇野ASCは、レンズ表面の蒸着膜の上に、空気を含んだ膜を形成する最も新しいコーティング技術で、2014年に開発されました。蒸着膜層と外気の間に「空気を含んだ膜」を挟むことで光の反射を抑え、特に垂直に近い角度で入射する光に対して高い効果を発揮します。また構造体を持たないASCは、適用できる面の種類がSWCより豊富です。適用する面の自由度を広げることは、重要な開発目的の一つでした。
ASCの構造
-
-
ガラス(コーティングなし)
反射率の高いガラス面のみの場合、入射する光の多くを反射してしまいます。 -
-
ASC(超低屈折率層+蒸着膜層)
ASCを施すことで、光の反射を抑制し、クリアな描写を実現します。
SWCは斜めからの光に有効で、ASCは垂直に近い光に有効ということですが。
槇野原理から言うと、光が上から来ようが横から来ようが、くさびは光にとって境界面にならず、境界面がなくなれば反射防止性能は突出して良くなります。ですからSWCは、斜めからの光だけでなく垂直に近い光に対しても抜群の性能を発揮します。特定の光に特化したものではありません。
一方、ASCは境界面を持つものなので、斜めからの光の反射防止性能に関してはSWCの方が上ですが、ASCの膜は垂直に近い光に対して高い効果を発揮する構成としています。
そうすると、SWCとASCのすみ分けはどのようになりますか。
槇野フレアやゴーストをなくす技術が、どういうところに必要なのかということにもつながってくるのですが、斜めからの光に対する性能が必要なレンズにはSWCを、それ以外のレンズにはASCを積極的に入れるということになります。
ASCのポイントについてもう少しお聞かせください。
槇野外気と膜との境界面での反射を小さくするために、超低屈折率層を開発しました。一般的な膜材料だと、低屈折率な膜の屈折率は「1.37」程度です。空気の屈折率が「1」なので、空気に近づけ反射を小さくするには、SWCのようにくさびを使って外気と膜の境界をなくすという発想を除けば、膜の中に空気を含ませるしかないという結論に達しました。そこで空気を膜の中にどれだけ含ませることができるか、という話になりますが、ASCは、小さなサイズの空気を膜に無数に含ませるという方法を採りました。
一つひとつの空気のサイズが大きすぎたり、分布が不均一になったりすると、膜に含ませた空気自体が光の乱反射の原因となって光が透過しづらくなり、反射防止膜として使えません。また、空気の量が多すぎると膜が脆くなってしまいます。
ASCは、材料の組成やプロセスで、空気のサイズや量を制御しているところが技術的なポイントです。私は材料とプロセスの両方に関わっているので、性能と反射防止膜形成後のレンズの取り扱いのバランスを考慮し、双方を詰めていくことに最も苦心しました。
やりがいを感じるのはどのようなときですか。
槇野反射防止膜はナノレベルで目に見えず、性能が良くなるほど存在が見えにくくなるという地味な技術ですが、例えば「EF11-24mm F4L USM」のような従来では実現できなかった、超広角の焦点距離という特長をもつレンズを製品化できる、つまり従来は撮影できなかった写真が撮れるようになる、という写真文化にも大きな影響を与える技術です。そして、そのような新しいレンズ製品を使っていただいたお客さまに高い評価をいただいたときに「やってきて良かった」と思います。
SWC、ASCのように性質の異なる独自の高性能反射防止膜を2種類も持っているのは、現時点*では業界の中でもキヤノンだけです。私たちの開発はこれらを上手に使い分け、より高性能なレンズを作ることに向かって進んでいます。
* 2018年6月時点
エンディング
消費者の手に新製品を届けるためには、製品そのものの開発だけでなく、量産品として、その製品をどのようにして形にするかという「生産技術」が不可欠だ。キヤノンの生産技術は、材料開発から加工・成形、製造装置の開発まで製品開発に関わるあらゆる分野と工程に携わり、画期的な技術開発によって、世の中になかった新しい製品を多くの人に届けることに貢献してきた。
そこには必ず、何度トライ&エラーを繰り返しても諦めない開発者魂があった。難しい挑戦ほど楽しいと感じる技術者の感性があった。開発者たちのあくなき挑戦は、創造の可能性をどこまでも広げ、これまでになかったものを生みだす原動力となる。優れた生産技術は光学技術のさらなる進化を支え、「見たままを撮りたい」という想いに今後も応え続けていくだろう。
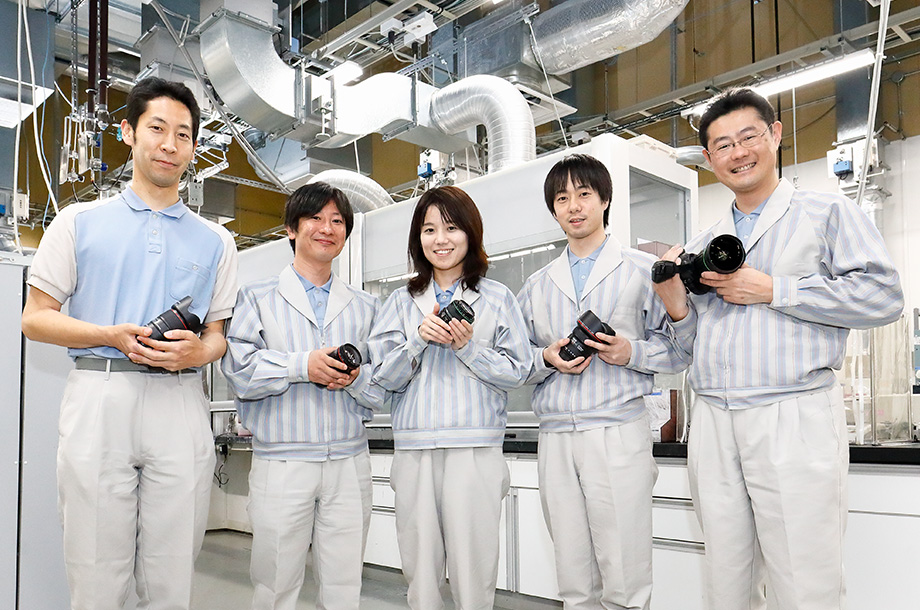
インタビュー・構成 : 後藤依子(ごとう よりこ) 印刷会社、編集プロダクションを経て、フリーのディレクター・ライターとして独立。半導体、エネルギー、工業機器、環境など、幅広い分野で執筆業を中心に制作に取り組む。