Service for Semiconductor Lithography Equipment
Lithography Plus
“Lithography Plus” is a solution platform offering Canon’s support know-how to help maximize productivity for semiconductor lithography systems.
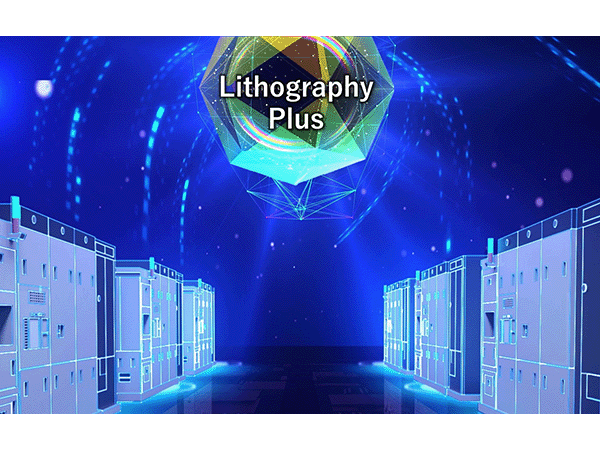
- Features
- Specifications
Basic Information
Service Name: Lithography Plus
Features
1. Canon’s Lithography Plus system includes functions that analyze the status of lithography systems, results of regular maintenance, causes of system downtime and other valuable information. System users can utilize this data to more easily create system operation plans during maintenance or parts replacement, thereby enabling appropriate maintenance. What’s more, the Dash Board function helps to further increase the efficiency of user maintenance work by providing a holistic view of all semiconductor lithography systems in operation at their worksite.
2. The Anomaly Detection function supervises system operational status and detects abnormalities and signs of potential trouble to prevent unexpected system shutdowns. In addition, an Automatic Restore function helps restart system operations. When automatic restoration is not possible, system restoration instruction are presented to operators in an easy-to-understand manner, thereby facilitating smoother recovery. What’s more, through a remote concierge service, system status can be shared with Canon’s expert engineers, helping them better understand the situation at hand and provide detailed assistance during customer support calls.
3. The Process Solution function provides a comprehensive collection of successful lithography system optimization recipes that Canon has accumulated over its long history in the business. By providing automated and optimized “recipes*1” for configuring such settings as precise alignment accuracy and control of line width, enabling even newly implemented semiconductor lithography processes to realize high yield rates*2, thus supporting increased system productivity. Lithography Plus also has the ability to interface with APC*3 and other process equipment, making possible greater coordination with manufacturing management systems.
- *1. Manufacturing conditions that vary depending on the device and type of manufacturing process.
- *2. The ratio of properly formed products to defective products in a manufacturing process.
- *3. Advanced Process Control. Refers to the use of optimized processing parameters for individual lots. Results of past processes are applied and used for such purposes as predicting values in front-end processes, advanced statistical and analytical techniques to manipulate process control parameters and inputs on process tools to improve output quality.
Specifications
Target model | FPA-6300ES6a、FPA-5550iZ2 (as of Sept. 2022) |
---|---|
Operating environment | Web application system using server client system![]() |
Server configuration | Application server, DB server, each installed by Canon |
Client | Prepared by the user. PC running Chromium-based web browser Screen resolution 1920 x 1080 |
Number of connected tools | 10 devices per 1 DB server, 10 servers per 1 AP server |
Data Retention Period | 3 Months (Standard) |
Tool administration efficiency | - Dash board function to display details of equipment status - Throughput calculation and improvement simulations - Alignment, focus and overlay accuracy prediction and improvement simulation |
Enhance tool availability | - Anomaly detection, failure detection and automatic recovery - Recovery procedure documents*1 - Remote service*2 |
Higher yield | - Automatic recipe parameter optimization functions |
- *1. Depending on the failure, appropriate procedure will be displayed
- *2. Secure network is necessary between customer and Canon service office