Product Responsibility
Quality Management
Approach to Quality
In 1964, Canon determined that its basic quality concept* is to ensure that customers have “no claims, no trouble,” and has since striven to earn the trust and heartfelt satisfaction of customers around the world by providing products and services of surpassing quality. Based on this mindset, the Canon Group’s firm commitment is to adhere to the Canon Quality motto that incorporates the three keywords “Safety + Smartness + Satisfaction” —the elements we view as essential to product and service quality. We are dedicated to improving the quality of products and services over their lifecycles.
- * “To contribute to the growth of the company and prosperity of the world, with the realization of ‘no claims, no trouble’ as our goal, based upon the company’s corporate philosophy and aims.” (Canon Quality Assurance Basic Regulations, Article 2)
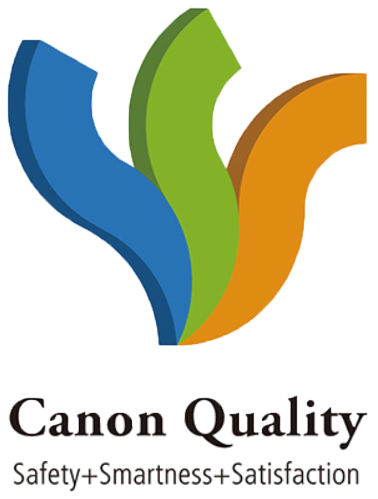
Quality Assurance System
At Canon, we have developed an in-house quality management system that we follow assiduously. The system has three defining characteristics, as outlined below.
-
Fulfills all the requirements of the international quality assurance standard ISO 9001*1
-
Incorporates the concept of “substantial safety*2” as standard for quality management
-
Introduces a framework for checking quality in product commercialization processes to ensure reliable product safety standards*3
Using our in-house quality management system as a base, the various Headquarters divisions at Canon implement rigorous quality control by building quality assurance (QA) systems that are optimized for the characteristics of each business, as well as in compliance with the legal and regulatory standards of each country and region.
Under Canon’s quality governance set-up, the quality assurance division within each business division works independently of the development and manufacturing divisions. The Global Quality Management Office, a separate entity reporting directly to the CEO, also oversees quality assurance activities by each business division.
- *1 The in-house regulations governing Canon’s quality management system are recognized by the International Register of Certificated Auditors (IRCA) as an alternative standard to ISO 9001.
- *2 This means safety not only in terms of what is required by laws and statutes, but also any safety issue that can reasonably be expected to arise during customer use even if not regulated or mandated by law.
- *3 This involves setting QA standards that must be satisfied for each of the stages in the development of Canon products from development and design to production and shipping. At each checkpoint along the development path, the QA framework requires a decision on whether the QA standard is satisfied to ensure rigorous control of product quality.
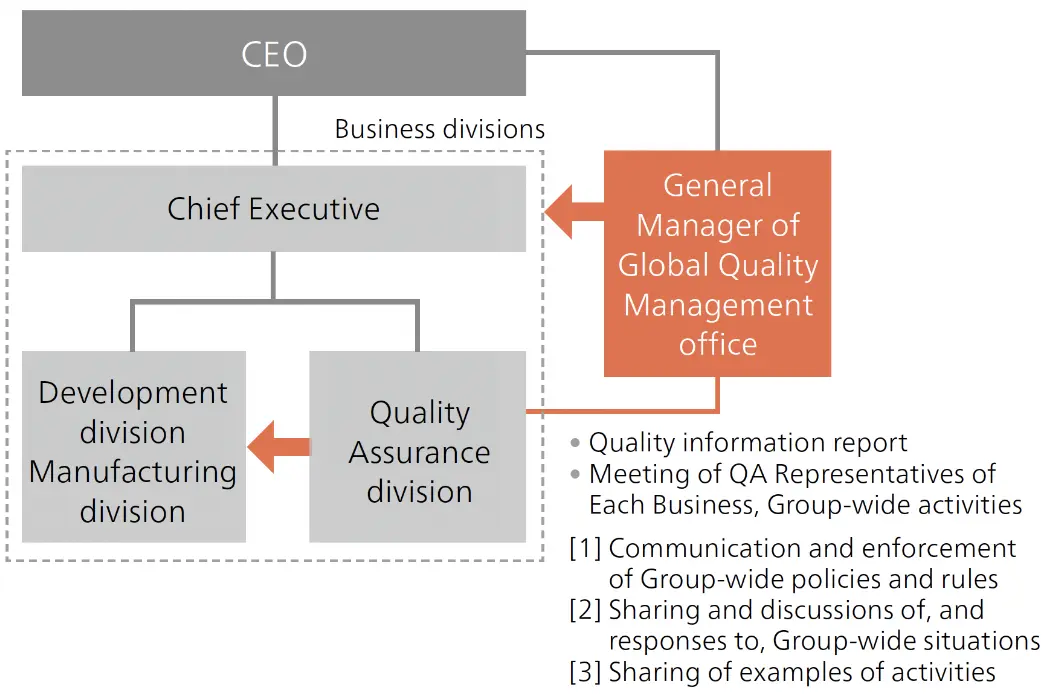
Education and Raising Quality Awareness
Canon employs a range of measures to instill high employee awareness of the need to maintain outstanding quality and attain further quality improvements, and to help employees gain related knowledge.
We continually communicate our basic concept and motto on quality, while also conducting annual Group-wide surveys of employees to ascertain the degree of quality awareness. We have designated November as Quality Month, and each year in November hold the Quality Fair and Quality Awards to raise quality awareness and recognize exceptional activities that have improved quality.
In addition, we provide online educational courses on quality for all employees and have developed a tiered training curriculum for Group companies in Japan and abroad. Alongside this, we have training programs customized to the specific circumstances and issues of each division, and we also conduct on-site training at production sites.
We also focus attention on training related to product safety, including a wide range of online and other training courses aimed at all levels from new employees to managers on product safety regulations and technology used in creating designs for safe products.
In 2024, we invited an outside expert on the serious quality issues uncovered at other companies to give a lecture to directors and all senior managerial staff at Canon Inc. on how to prevent such quality issues.
Training Completion for Canon Inc. (2024)
- Basic Online Course on Quality (6 parts): 14,245 people
- Tiered Course on Quality (new employees, general/managerial staff): 6,920 people
- Online Course on Product Safety Regulations (4 parts): 9,081 people
- Training Course on Technology for Safety Design (4 parts): 147 people