What is in-house production?
In-house production refers to the idea of reclaiming procedures and processes that were previously outsourced. It is the opposite of outsourcing, which has traditionally been used as a cost-cutting measure, or in cases where a company lacks the resources (typically workers, machinery, technologies or other expertise) required for a specific process.
At Canon, we see in-house production as vital to our mission to use technology to create a suite of innovative and distinguished products and services with high added value. To this end, we are actively promoting the shift to in-house production throughout the Canon Group. In-house production delivers a host of benefits: new technical knowledge and expertise; shorter product development lead times; cost savings; better product quality and consistency; and improved security for sensitive corporate data. At the same time, it is not feasible to perform every aspect of our operations in-house. Thus we need to carefully define the scope of processes and procedures that can be brought in-house, taking into account potential benefits in terms of distinguishment, production costs and quality standards.
If monozukuri doesn’t change and evolve, our products won’t improve
The move toward in-house production even extends to the development of production and processing systems for key parts and components that have a major bearing on product performance. Lenses are a good example of a key part for which Canon innovation has played a major role. Ultra-long telephoto lenses, commercial broadcast quality lenses and high-precision aspherical lenses for semiconductor exposure equipment all utilize highly advanced machinery for cutting out glass pieces and then grinding and polishing the glass surface to an incredibly high level of precision—surface smoothness is often measured at the nanometer level. Canon has designed and created its own processing and measuring equipment to deliver this standard of precision because it simply cannot be found elsewhere. As testimony to this level of production excellence, our lenses were selected for the Subaru Telescope at the National Astronomical Observatory of Japan (NAOJ). In such ways, Canon has drawn upon our experience and expertise in the area of lenses to create highly advanced production systems that in turn produce innovative and competitive lens products.
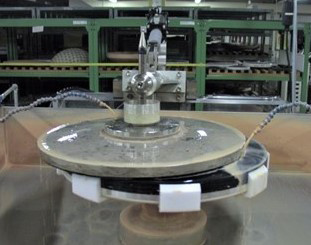
Prime-Focus Corrector for the Subaru Telescope made by Canon
Making products that nobody else offers
Canon boasts considerable technical expertise in electrophotography, the core technology used in laser printers and office multifunction devices. Transferring the powdered ink known as toner onto individual sheets of paper quickly and precisely, whether in a laser printer or a multi-function device, requires myriad parts including the charging roller, developing roller, transfer roller, cleaning blade, transfer belt and fixing belt. All of these key parts are required to move at high speeds and with a high degree of precision, so it is important to identify the properties expected of each one. This is achieved through in-depth analysis of the physical phenomena involved in every operating process, performed by highly skilled process engineers with a deep knowledge of how printers work. Canon often develops and produces custom materials that deliver the properties and characteristics required for specific key parts.
Canon produces a range of unique and customized high-performance components. Often this involves modifying the input material, such as resin or rubber, via chemical reaction, denaturing, blending or other techniques in order to achieve the particular properties required. Canon has also created a series of specialized molding processes for fabrication of rollers, blades and belts. Of course, it takes a great deal of time and effort to develop the technology behind precision lenses and electrophotography. But it is Canon’s commitment to product differentiation that serves as the foundation for the move to in-house production.
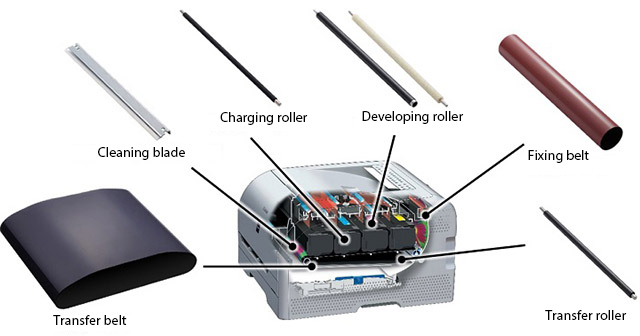
Laser printer key parts