Product Responsibility
Initiatives
Ensuring Product Safety
Voluntary Action Plan Based on the Basic Policy on Product Safety
Canon Inc. believes one of its important missions as a manufacturer is to provide safe products to customers. With this in mind, we formulated a Basic Policy on Product Safety that Canon Group companies strictly adhere to.
Based on this policy, Canon Inc. and Group companies formulate and follow individual Voluntary Action Plans for Product Safety suited to their business format, working to ensure product safety while remaining customer-focused.
Besides using online training courses to help ensure such information is disseminated and followed, we continually update every Canon Group company involved in the sale, repair or servicing of products with the latest safety information for repairs and part exchanges.
Moreover, we comply fully with government laws and notices, and have developed a system for immediate reporting, for example, in the unlikely event of an accident involving one of our products.
2024 Activities Scorecard for Canon Inc.
- Carried out review by senior management based on the Voluntary Action Plan for Product Safety (conducted annually since 2008)
- Continued efforts to raise awareness among customers about smoke emission from counterfeit batteries and the safe handling of electric cords and plugs, etc.
- Continued implementation of product safety training and emphasis on the importance of product safety during basic training on quality
- Continued implementation of e-learning course for all employees to promote understanding of the Voluntary Action Plan for Product Safety
- Revised the internal standards relating to product / chemical safety
Establishment of In-house Product Safety Technical Standards
Canon has established its own safety standards (for substantial safety) for all Canon products, which take into account customer safety as well as legally stipulated product safety standards.
For example, Canon’s safety-conscious standards call for the use of plastics that are more flame resistant than the law requires, and we implement double-protection schemes for important safety-related components.
We regularly revise these standards in light of technological advances as well as changes in how customers use our products, and changes in customer demands regarding safety.
We use our proprietary safety standards to apply rigorous quality controls to all products within a framework for checking quality across product commercialization processes. Ensuring that all our products are safe to use, we never release to market any product not meeting the standards.
Main Approaches to Safety Technology
- Conduct safety assessments that address human factors (physical function, abilities, thinking and behavior), taking into account the variety of possible operations a user may perform
- Conduct safety-confirmation testing based on abnormal voltage waveforms in commercial power supplies confirmed at marketing sites in each country and region
- Hypothesize abnormalities, such as glitches or malfunctions, and conduct stricter safety-evaluation testing than is required by the laws of each country or region
Quality Assessment During Development
Creation of Assessment Environment for the Delivery of Safe Products
Canon has testing facilities for accurate and detailed evaluation of all aspects of product safety in line with official standards and any applicable laws or regulations, including the measurement of chemical emissions, noise, biological safety, EMC*1, and flame resistance ratings.
ISO and IEC*2 accreditation enable Canon to use in-house facilities for the rigorous testing required to apply for safety/environmental labels for Canon products worldwide. This includes one of the largest, most advanced electromagnetic anechoic chambers in Japan, as well as various other world-class facilities. High-level, reliable quality evaluation is built into Canon’s product development process.
- *1 Electromagnetic Compatibility testing. Testing for electromagnetic interference caused by a product or its power source that may affect the operation of other equipment, and testing for electromagnetic susceptibility of the product itself that may result in malfunction.
- *2 International Electrotechnical Commission, an international standardization group that formulates standards on electrical and digital technologies.
Varied Safety-oriented Initiatives
Safety Assessments of Chemical Emissions from Products
Canon assesses the chemical emissions from its printers, multifunctional devices (MFDs), and other products. Our assessments include measurements of data necessary for acquisition of Germany’s Blue Angel environmental label.
To ensure the safety of customers using Canon products, we have also defined our own internal safety standards based on the guidelines for indoor air quality and indicators as set by major bodies in Japan, the US and Europe, along with the related international standards. We also check that our products conform to these standards.
The in-house laboratory conducting these assessments has received accreditation from Germany’s Federal Institute for Materials Research and Testing (BAM) and is therefore capable of conducting the assessments required for applications for Blue Angel certification.
It has also received ISO/IEC 17025 accreditation to conduct measurements in a fair and neutral manner.
Our evaluation protocols appropriately reflect the most up-to-date knowledge, such as the adoption of the ISO/IEC 28360-1 international standard for measuring chemical emissions, which was revised in November 2021.
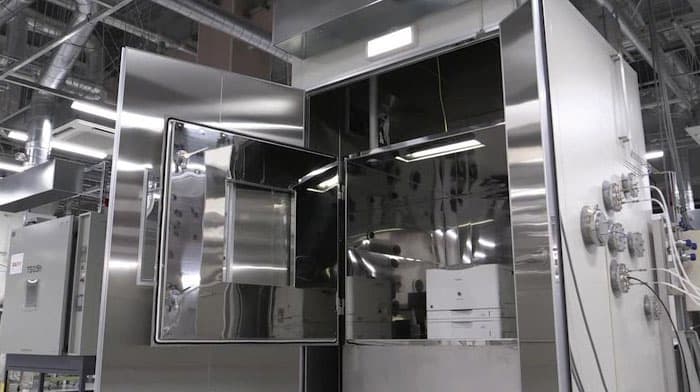
Biological Safety Assessments for Ink, Toner, and Other Consumables
Canon assesses the safety of its ink, toner, and other consumables, enabling customers to use its printers and MFDs with confidence.
For example, with regard to the materials for ink and toner, we carry out assessments related to genotoxicity, thought to be closely linked to carcinogenicity, using bacterial reverse mutation tests and in vitro mammalian cell micronucleus tests.
Canon’s testing laboratories are highly reliable and have been certified by Japan’s Ministry of Health, Labor and Welfare as in compliance with Good Laboratory Practice (GLP)*1 standards in the Act on the Evaluation of Chemical Substances and Regulation of Their Manufacture, etc. (Chemical Substances Control Law). Canon’s laboratories also comply with GLP standards set by the Organization for Economic Cooperation and Development (OECD). Furthermore, Canon became the first in Japan to have its in vitro mammalian cell micronucleus test certified as in compliance with the GLP standards in the Chemical Substances Control Law.
Canon is actively working on the use of alternatives to animal testing in chemical safety assessments. Besides researching and utilizing information on Integrated Approaches to Testing and Assessment (IATA) including the use of alternative testing data*2, we are making progress in conducting in-house testing according to OECD Test Guidelines.
- *1 The standard for the management, testing and reporting of facilities and organizations that operate as testing agencies conducting chemical substance safety assessments. Testing according to GLP standards ensures reproducibility and data reliability. GLP standards set by the OECD were enacted in 1981, and since then, member countries have developed domestic laws and regulations based on these standards. Facilities certified as compliant under Japan’s GLP standards in the Chemical Substances Control Law must have their certification renewed every three years, which involves receiving a new conformity screening prior to the expiration of the certification’s validity period.
- *2 Canon does not conduct animal tests on ink, toner, or other consumables, unless required by laws or regulations, or requested by authorities, or where such testing is essential to safeguard customer safety.
When conducting animal tests, we must comply with the “3Rs (Three Rs),” which are the basic principles of animal testing worldwide. This is stipulated in our internal rule regarding chemical safety.
Assessing the Safety of Medical Devices
Canon assesses the safety of medical devices based on ISO 14971 standards for the risk management of medical devices to ensure the health and safety of patients and users. For example, we do not simply identify hazards related to electrical, mechanical, or thermal energy in general. We also identify various related hazards such as biological safety, use error due to inappropriate usability, and cybersecurity, confirming throughout the lifecycle that anticipated risks have been reduced to an acceptable level.
Ensuring Quality and Reliability in Parts Procurement
Canon actively pursues activities to ensure the quality and reliability of procured parts and materials used in products, so that they can be used for years with confidence.
To ensure product quality, we have devised technical checklists by type for important procured components; we also maintain a quality assurance framework to ascertain the technical capabilities of suppliers prior to any new parts procurement. To enhance quality, we work together with suppliers to optimize quality control systems and manufacturing processes. We also utilize high-precision nondestructive analysis technologies such as X-ray CT scans and thermal analysis to evaluate electronic components and isolate defects. In addition, to detect and resolve quality defects at an early stage, we strive to apply and upgrade technical solutions based on chemical analysis to elucidate the causes of material degradation, component damage or contamination with impurities.
Product/Service Security Measures
Measures to Address Vulnerabilities in Canon Products/Services
Network connectivity via the cloud or smartphones is increasingly enhancing the benefits from Canon products and services. On the other hand, there is a growing need for measures against the increasing cybersecurity risks, including the risk of loss of personal information or confidential data. Canon focuses on the potential cybersecurity risks from the product development stage to prevent any problems. In case specific security issues are identified, a system is set up to prevent or mitigate any negative impact on customers.
Development Process
We formulate the security requirements for Canon Group products and services based on regulatory information and the technology trends adopted by industry bodies, software vendors and other parties.
The requirements are reflected in the development process by utilizing a secure development process that must include compulsory review checks and vulnerability testing. To prevent recurrence of past vulnerabilities, final quality sign-off requires prior completion of a vulnerability assessment stage within a company-wide process.
Education and Training
Product/service vulnerabilities response is a highly specialized area in which it is necessary to acquire and track the latest technical progress as well as increasingly sophisticated attack methods. Canon defines career and skill levels for its new software engineers, customer service engineers and security specialists, and has designed a level-specific security training curriculum to develop human resources. Support to the onsite vulnerability testing is provided as a follow-up to also build practical skills alongside the theoretical knowledge base.
Activities of Product Security Incident Response Team (Canon PSIRT)
We created the in-house Canon PSIRT team to respond to security issues as they arise in the field.
Working in the framework of METI’s Early Warning Partnership and collaborating with the external groups such as JPCERT*1 Coordination Center and FIRST*2, Canon PSIRT pays close attention to vulnerability related developments in the field, and gathers the latest information. Canon PSIRT website is published as a window to receive vulnerability information from researchers worldwide, and to release customer advisories on vulnerabilities of Canon products and services in a timely manner, thus ensuring cybersecurity response is on a world standard level.
- *1 JPCERT: Japan Computer Emergency Response Team
- *2 FIRST: Forum of Incident Response and Security Teams (a global community of cybersecurity incident response teams from government entities, educational institutions and companies worldwide)
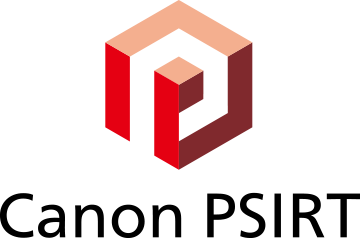
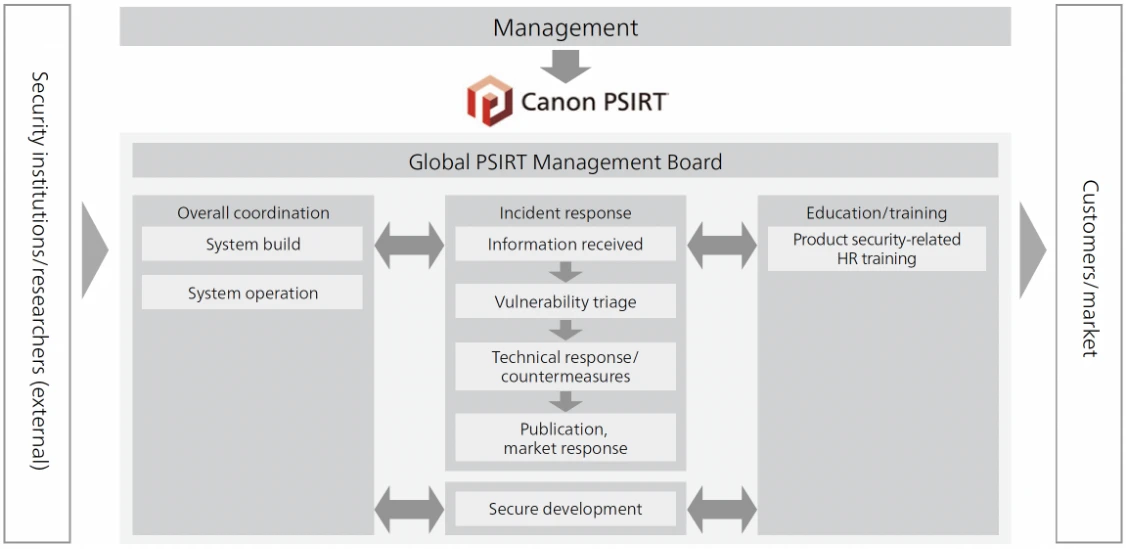
After-sales Support
Enhancing After-Sales Services in Various Countries and Regions
After-sales service is crucial to enabling customers to use our products with confidence. Canon is putting efforts into expanding the after-sales service network to be able to provide the same level of prompt, reliable support anywhere in the world.
For example, to enhance customer usability and more easily resolve issues, we are expanding customer support services globally through our website. In addition to posting FAQs, product specifications, user manuals, and other support information, the latest driver software is also available for download. Support information and software are both based on content shared worldwide, while including needed local content for each country or region. Group marketing companies then localize the content in various languages.
We continually monitor how customers use content and analyze survey responses and other data, feeding back the results to divisions producing content to constantly make updates and improve customer usability. We are also working to offer more user-friendly services by optimizing content to support the greater use of a wider range of information devices.
Market Information Collection and Analysis, Feedback
In order to achieve even greater customer satisfaction, Canon conducts product evaluations from the customer’s perspective at the development stage, and incorporates customer feedback and requests in its development and design processes.
For example, using a framework called the Call Information Collection and Analysis System, we built a database of customer feedback and requests received by call centers at our marketing companies worldwide, and manage this data centrally. Development divisions take advantage of this data to enhance customer usability, such as improving display methods on product control panels or simplifying the steps needed to connect to wireless LAN. Information gleaned from customers is shared internally throughout the Group, including development divisions, production divisions and marketing companies, and used to improve each local site.

Process for Responding to Quality Issues
Should a quality issue arise, Canon has systems in place to promptly and appropriately investigate the cause, repair products free of charge, and disclose quality information. We also keep our customers informed about product quality issues and remedial procedures by placing product advisory statements in various newspapers and on our website.
There were no such statements in 2024. Should a quality issue arise, our marketing companies in each country or region, which serve as the contact point for customers, file a report with the quality assurance division of the respective Canon Inc. Headquarters division (products operations). The quality assurance division then investigates the cause of the issue as well as countermeasures. Moreover, in the event of a major issue, related Headquarters divisions (products operations), the Global Quality Management Office , legal division, and public relations division are consulted concerning response measures, and after the matter is reported to the CEO, action is promptly taken.
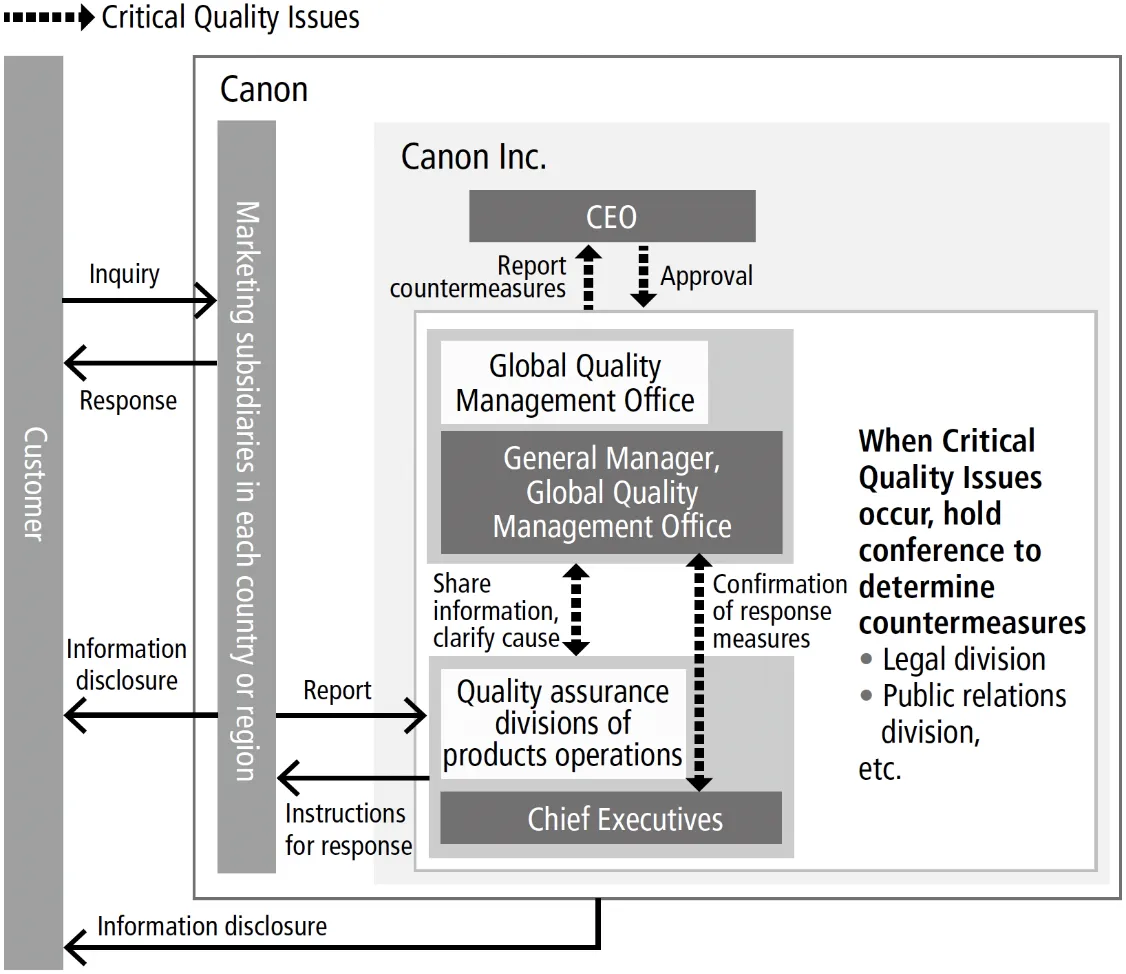
Improving Product Usability
Providing Information on the Appropriate Use of Products
Pursuing Usability for Canon Products
From consumer products to industrial equipment, to ensure the greatest possible ease of understanding and use for customers with a wide range of needs, Canon carries out usability tests using both internal and external monitors, web-based surveys, and expert staff evaluations at the product development stage.
We objectively test human factors, including physical characteristics, perception, judgment, and operating burden, to develop products that customers can use comfortably and with ease. We built a dedicated monitoring test room equipped to allow detailed observation and recording of the behavior and actions of testers as they operate devices, including even hand movements.
Moreover, we are working to create safer testing environments by implementing measures to prevent infection such as a mechanism to broadcast testing scenarios for remote observation and the installation of clear plastic panels to block air-borne droplets.
Promoting Universal Design
Canon strives to develop people-friendly products by pursuing functionality, operability, and convenience from the customer’s perspective in actual usage situations. As part of this effort, we have adopted a universal design approach through which we endeavor to create products from a customer perspective from the design stage onward, facilitating use by all customers, regardless of age, gender, nationality, or physical ability. At Canon, we approach product design and development from the perspective of making the customer “look like a natural.”
For example, we evaluate and test usability, accessibility, and comfort from various perspectives, regarding aspects such as text sizes that are easy to read and color designs that are easy to recognize for people with various visual sensitivities. Information obtained from these activities is valuable in the development of more user-friendly products.
Moreover, aiming to encourage efforts in universal design, we distribute a guidance booklet to all development divisions that addresses the physical characteristics of users and various other issues that arise during product use, and also conduct e-learning courses to enhance knowledge in this area. We also create customer-oriented pamphlets and post website content among other steps to share information both inside and outside the company about the universal design initiatives underway at Canon.
Universal Design Action Guidelines
- Ease of use in every aspect
Beginning with a complete understanding of customers’ usage scenarios, we use every means in our designs to provide usability suitable for the customers’ usage objectives and situations. - Aim for products and services that people want to use
We seek out and generate innovative ideas that go beyond mere improvements in order to create products and services that customers naturally want to use. - Put the latest technologies to use
We take advantage of Canon’s most advanced technologies to enhance customer convenience and realize richer and more comfortable living and working conditions.
Product Accessibility
Canon is working to increase the accessibility of its products in order to make them easy to use for the elderly and persons with disabilities.
Section 508 of the United States Rehabilitation Act requires that agencies of the federal government only purchase products that meet stipulated accessibility standards. The results of Section 508 accessibility evaluations of Canon products have been collected into a VPAT* and made available on the Canon U.S.A. website. To facilitate ready access for our developers, content on Section 508 stipulations is also made available internally in the form of Accessibility Evaluation Guidelines. Over in Europe, the European Accessibility Act, an EU Directive, was promulgated in 2019. European Standard EN 301 549, which is consistent with Section 508 standards, is now beginning to be adopted for government procurement, not only in Europe but also globally.
Canon is committed to continuously gathering the latest information, and to developing products that are compliant with the accessibility requirements of each country and region.
- * Voluntary Product Accessibility Template, a document that evaluates how accessible a particular product is according to Section 508 standards.