Redesigning the MFD from the ground up in pursuit of user convenience
A behind-the-scenes look at the development of the imageRUNNER ADVANCE Gen3 office multifunction devices
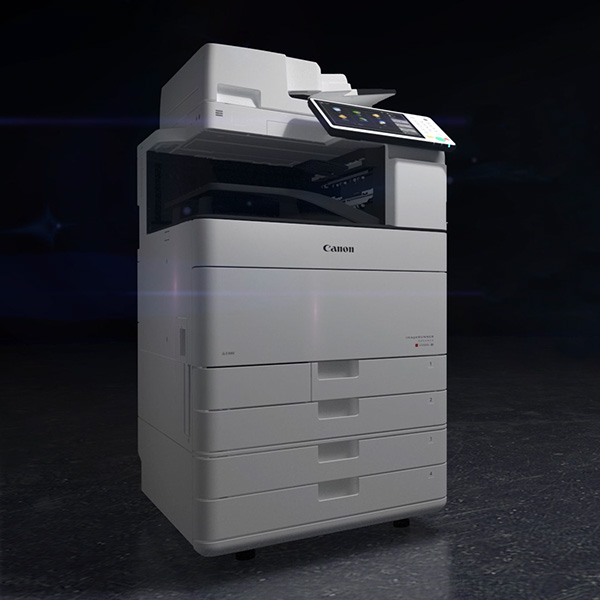
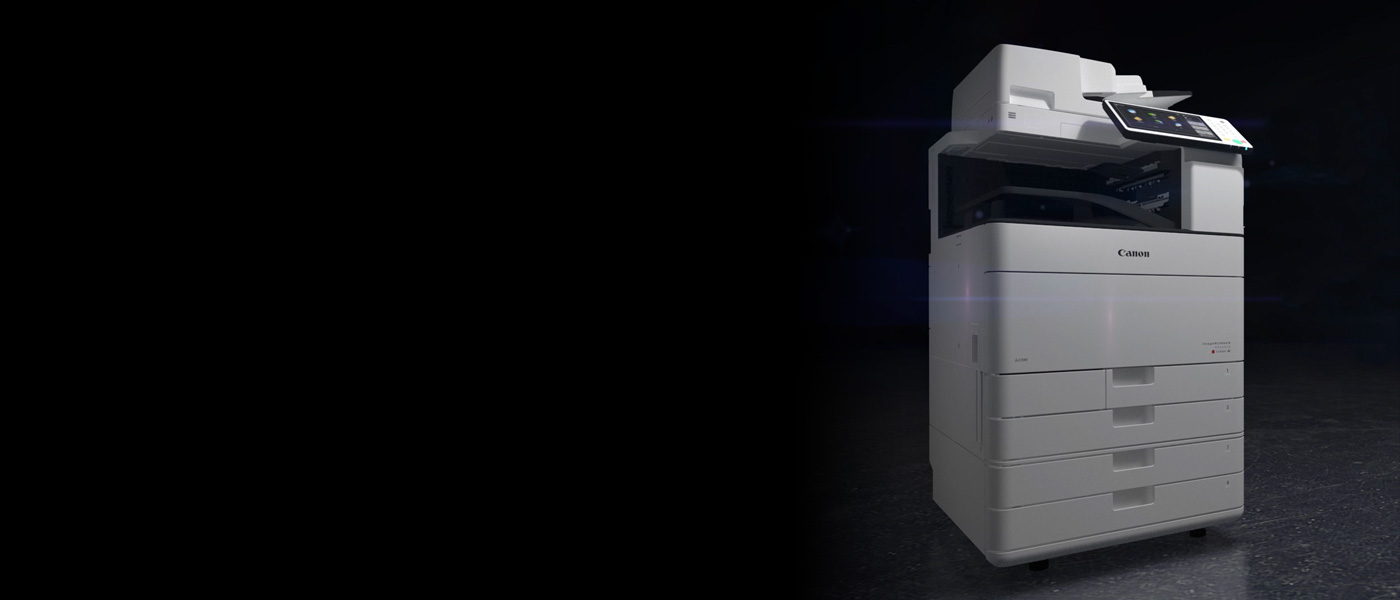
Canon's new multifunction devices (MFD) for office use, the imageRUNNER ADVANCE Gen3 Series, is the result of development based on extensive research and testing in all aspects--including design, operability, functionality, speed, quietness, image quality and security.
The project is noteworthy due to its key development concept--the thorough pursuit of customer convenience--under which development started entirely from scratch. Canon MFDs have continued to add new functionality in line with the changing needs of the office, and in 2009, adopted the series name of imageRUNNER ADVANCE. Now, the third generation, imageRUNNER ADVANCE Gen3, introduces its greatest-ever leap forward in functionality, including major advancements in security and cloud services.
The development team pulled out all the stops to meet their ambitious requirements for user convenience.
Developers interviewed
-
Masaki Maeno
area of expertise: mechanical engineering -
Tetsuhiro Yoshimoto
area of expertise: electrical engineering -
Takanori Iida
area of expertise: physics & chemicals -
Takeshi Hokiyama
area of expertise: software & security -
Shota Shimizu
area of expertise: software & security -
Kenta Inoue
area of expertise: software & cloud systems
01
A focus on image qualityA cutting-edge electrophotography system that prints clear and vivid images on any paper type
read more
-
- Takanori Iida
Since joining Canon in 2008, Iida has worked on physical process development for MFD print engines.
Motto: Be cheerful, positive and optimistic
On his off time: Playing with his kids, golf, reading
What kind of image quality is expected of today's MFDs?
Takanori IidaAs you know, MFDs print a lot of business documents, so the black text needs to be sharp. What's also important is that, more than reproducing an original image's colors and gradations, photos and images need to be vivid and clear. That's why I was particularly focused on achieving vividness that creates a sense of realism.
A photo printed by a Gen3 MFD.
- The wood's texture is realistic, while the grass feels fresh. The scene's greenery is vividly represented.
-
- By expanding the printer's color gamut, the scene can be reproduced more vividly.
-
- Sharpness control is used to enhance the edges of grass and leaves.
I also wanted make this possible on all types of paper. There's a seemingly endless variety of copy paper, and though they may appear similar, each is quite different. As such, producing the same result on all kinds of paper can be difficult. For example, the surface of recycled paper only looks "a bit rough" to the naked eye, but a microscope will reveal that it’s in fact very uneven. This means that toner has trouble adhering to the paper, which results in lower image quality.
It must be difficult to achieve the same vivid image regardless of media.
The electrophotographic process
-
1
ChargingThe photosensitive drum surface is negatively charged with a static charge.
-
2
ExposureLaser beams scan the photosensitive drum to form an image. Areas exposed to the laser beams lose their electrical charge.
-
3
DevelopingToner is brought in close proximity to the drum and affixes to non-charged areas.
-
4
TransferThe photosensitive drum is brought into contact with the paper and a positive charge is applied from behind, transferring the toner onto the paper.
-
5
FixingHeat and pressure are applied to fix the toner to the paper.
IidaMFDs use "electrophotography", which comprises five major steps: charging, exposure, developing, transferring and fixing. During the transfer process, an electrical voltage is applied to transfer the images created on each color's photosensitive drum onto the transfer belt. The resulting CMYK four-color toner image is then transferred to the paper by applying an opposite voltage.
In order to produce vivid images regardless of paper type, the transfer process is crucial. When the toner is transferred from the photosensitive drums, the transfer belt surface must possess electrical characteristics that maintain the toner image as received, while simultaneously possessing chemical characteristics that improve toner separation from the belt to the paper's uneven surface. We took a fresh look at the transfer belt--right down to the raw material level--and through this dedication, we managed to succeed in coming up with a design that possessed these conflicting characteristics.
We also fundamentally improved the toner. Seventy percent of an MFD's energy consumption comes from the fusing process, so increasing thermal efficiency is a must if we want to improve productivity and energy efficiency. One effective solution is to make the toner melt more easily. However, altering the toner in a laser printer means we need to reconsider the entire process design--voltage, drive timing, etc. That's a risky strategy, as it drastically extends development time. Nonetheless, because our customers wanted greater energy efficiency, I felt we had to change the toner.
In what way did you need to change the toner?
IidaWe essentially switched to "hard but easy-melting toner". If the toner easily softens at low temperature, we run the risk of it all clumping together if it gets hot during storage or transportation. We wanted the toner to melt easily under low temperature, but prevent it from clumping when stored in hot environments, so we came up with the idea of giving the toner particles a tough outer shell structure, while allowing the inner core to easily soften.
-
- Toner cross-section diagram
-
- Low-melting-point toner
The aim of this project was to meet our customers' requirements, and we accomplished this by setting ourselves the difficult goal of developing toner that could produce sharp and vivid pictures on any kind of paper, while remaining energy-efficient and highly durable. We accomplished this “outstanding” laser printing system, so to speak, by starting from scratch rather than just making improvements.
What in particular was your priority when starting from scratch?
IidaI work in the Process Design department, which is primarily responsible for determining specifications related to image formation. We do this by first clarifying the characteristic and target values of each step in the electrophotography process before commencing simulations and testing. When we're setting the targets we want to achieve, we need to be able to communicate clearly and effectively with other departments including mechanical, electrical and software engineering. Since the concept was “the thorough pursuit of customer convenience.” I think we were all on the same page in setting the targets we needed. Our teamwork is powered by each individual's strong desire to achieve difficult goals. There were many long, difficult days before development was wrapped up and the product was finalized, but seeing the first machine roll off the production line made me really happy.
02
A focus on mechanical design for ease-of-useHow to make a printer so quiet you hardly know it's there and achieve significant operational speed improvements, even during user authentication
read more
-
- Masaki Maeno
Since joining Canon in 2008, Maeno has worked on MFD print engine mechanical development.
What I like about Canon: Being able to work flexibly. Making suggestions and being able to make them reality
What thrilled me most since joining: Seeing my work receive high praise in the market.
What did you focus on most during hardware development?
Masaki MaenoMFDs are meant to help our customers do their jobs better. As the whole project team's objective was “The thorough pursuit of customer convenience,” we focused on three factors in particular: (1) Quiet operation that helps the device blend into the office, (2) Industry-leading speed to minimize user wait time and (3) Ensuring high image quality with every print. We worked on enhancing core performance to such an extent that users notice a clear improvement.
Noise is something you can measure using numbers, of course, but it's also quite a sense-related thing. We felt it would be ideal if everyone other than the person using the machine didn't notice it operating, so that's what we aimed for.
We set out to achieve a quieter design, using cutting-edge measurement techniques to digitize the sound and perform simulations. In particular, we focused on fixing loud, unpleasant sounds in order to keep the noise level contained as consistent as possible.
Rather like air conditioning, in a way; it can be quite loud when it first turns on.
MaenoYes, exactly. Air conditioning always makes noise, but you only notice it when the noise level increases. That's why we focused not only on the noise itself, but also the acoustic quality and fluctuation in noise volume, to ensure that the noise is less noticeable.
MFDs perform a variety of operations simultaneously before the document arrives in the output tray. They scan the original document, feed paper, supply and deliver toner, fix the toner to the paper using heat and pressure, then perform post-processing such as stapling. There are many noises: for example, the sound paper makes when passing over a bump, the sound of air flow and the click sounds of mechanical parts make when operating. That's why it wasn't so easy to realize the solution was to reduce the intensity of individual noise sources.(←削除)
In addition, as you make things quieter, the noise from louder components becomes more noticeable. Because of this, all the departments had to work together in order to make the completed product quieter. The mechanical, product, electrical and software design teams all worked together to address each and every noise. As development progressed, I felt the teams' sense of trust and unity improve.
How Gen3 has reduced noise
-
- Tetsuhiro Yoshimoto
Since joining Canon in 2005, Yoshimoto has worked on electrical design development of MFD print engines.
What I like at Canon: How members from different departments cooperate and discuss how to solve problems.
On his off-time: Enjoys visiting izakaya (pub-style restaurants)
I think demand for faster operation is also a factor. How did you work on speed?
Tetsuhiro YoshimotoWhen we talk about speed, we used to refer to the time it took between the user pushing the copy start button and the paper arriving in the output tray. However, when noticed how customers were actually using the MFDs, we realized that this approach wasn't enough.
The way MFDs are used in offices is changing. Before, the user would command the unit to start printing from their desk computer, then get up and fetch the printed document. Now, a new style is emerging-–after commanding the MFD to start printing, the user walks over to it and logs in, then waits there for the printing to complete. That's why it's important that, from the point when the user gets up from their desk to when they pick up the printed document, they don't feel like they're kept waiting. Gen3 models are equipped with a motion sensor that detects when the user is approaching and starts up, ready for operation just as they arrive. This ensures the fastest possible process from the moment the user presses the print button. That’s why we needed to take another look at how fast the device wakes up from sleep mode, how fast it prepares to print, how fast it actually prints and so on.
The hardest thing was getting every startup operation to take place in parallel, rather than having each feature boot up sequentially. We managed to cut startup time in half by reexamining everything from scratch, investigating each component to cut microseconds off their operating times while working to have them initialize as simultaneously as possible.
Reduced startup time
When did you feel you had achieved a good balance of speed and quiet operation?
MaenoWhen we actually got feedback from the sales team that customers were not only noticing the speed but the quietness of the device as well, I was happy we had focused on achieving both. Our concept was clear about improving customer experience as much as possible, so in keeping with it we managed to achieve a balance of improving both speed and quietness and deliver enhanced comfort for the office and its users.
It looks like it was quite hard to get that balance right.
MaenoMFDs are full of moving mechanical parts, so there are many areas to be mindful of when trying to reduce noise. This project in particular was hard because we were also aiming to improve speed, so trying to achieve industry-leading quietness as well was a real challenge. But at the same time, rising up to face tough challenges with difficult goals was very rewarding. We improved efficiencies and smoothed out operations and paper flow bit by bit, and this led to us solving the problem.
YoshimotoIt really feels rewarding when you hit a wall and you’re faced with a difficult problem and manage to solve it. When you want to create a high-quality product, you set yourself tough goals, and when you consider that MFDs are a complex combination of a variety of technologies and elements, you’re bound to encounter several issues that are difficult to solve over the course of development.
How would you go about solving these problems?
YoshimotoMFDs are made up of various base technologies, which are developed concurrently by their respective teams. Each team is knowledgeable in their field, so when solving a problem, we pool our knowledge together and consider all the possibilities before making hypotheses. By then following these hypotheses together, we begin to solve the problem.
03
Focusing on users' security requirementsEnsuring MFDs are ahead of the security curve
read more
-
- Takeshi Hokiyama
Joined Canon in the year 2000 and has overseen MFD security development and security certification (Common Criteria certification) acquisition since 2013.
Motto: Positively considering any task as an opportunity to grow
Favorite book: How to Win Friends and Influence People by Dale Carnegie」
Enhanced security functions are a feature of Gen3, isn't that right?
Takeshi HokiyamaThere are two major aspects to security. One is to prevent internal information from leaking and the other is to protect the MFD itself from cyber attacks.
We added support for security information event management (SIEM) log management system to defend against data breach. SIEM is being adopted more and more throughout mostly large enterprises, with products available from such vendors as Splunk and McAfee. It works by storing standardized syslog messages from PCs, MFDs, telecommunications equipment and other devices in a SIEM server, allowing the system to detect malicious activity by applying detection rules set by the user in advance. If any anomaly is detected, an alert is sent to the IT administrator.
SIEM
For example, someone might be emailing scanned documents outside the company or making loads of copies late at night. Maybe a user has failed authentication multiple times. All of this is detected by SIEM, allowing administrators to take appropriate action.
-
- Shota Shimizu
Has overseen MFD security development since joining Canon in 2009.
What I like at Canon: Being able to work surrounded by engineers who are proud of their job
Favorite book: The Water Margin by Kenzo Kitakata
I've heard these models have a new feature called Startup Tamper Detection. Can you tell me a little bit about it?
Shota ShimizuCyber attacks are beginning to expand beyond PCs and servers, targeting mobiles and IoT devices. Network MFDs might be attacked too. To protect against such events, we developed Startup Tamper Detection, a function that enables the MFD to check if its own software program has been compromised.
During boot, Gen3 will validate the code stored on the MFD against the authentic code that was loaded during manufacturing and later updated to see if anything has changed. If it detects any modification, it will stop the boot process or automatically restore the illegitimate code to the authentic state. .If it has been seriously tampered with, we’ve programmed it to shut down and suspend operation until it is fixed by field service.
Doesn’t it take longer to activate the MFD as it checks for anomalies during start up?
ShimizuIndeed it does, so in the interests of balancing security with convenience, we worked hard to minimize the impact as much as possible. Security is critical, so we had to be certain we had covered all holes, but we searched for every millisecond we could shave off in the course of improving startup speed.
Did you include any proprietary innovations when implementing this feature?
ShimizuIn the field of security, being unique isn’t necessarily a good thing. A standard technology with underlying mechanisms that are open for all to see and yet not attacked, you can say that technology is quite robust. On the other hand, proprietary technology isn’t targeted in the first place due to its nature, so sometimes there could be "holes" that the developers failed to uncover. That's why we spent a lot of time closely investigating standard technology and technologies available from other vendors to see how we could customize them for Gen3 while ensuring there were no holes. Through a lot of effort, we were successful in eliminating vulnerabilities in the customized features of those technologies.
Ensuring security appears to be particularly difficult.
HokiyamaSecurity has always been important, but it never really been in the spotlight in the way it is now; I believe security has always been quietly considered an obvious requirement. Now that it receives a lot of attention, I feel the enhanced security in Gen3 is being well received by the market. At the same time, I’m even more conscious of the need to deliver products that give our customers even greater peace of mind.
ShimizuWe are of course thrilled that our customers are happy they have this security functionality, but I would have mixed feelings if they feel that way because they have suffered an attack before. Yes, it’s great that they were kept safe from the threat, but the very fact they were hacked at all is unfortunate. It’s rewarding as a developer to take on the challenge of advancing security, but I’d rather we could live in a world where it wasn’t necessary in the first place.
04
Focusing on the convenience only MFDs can providePowerful features are pointless if they're not easy to use
Cloud services for simplicity and convenience
read more
-
- Kenta Inoue
Has overseen MFD and its adjacent softwares' UX (user experience) since joining Canon in 2012.
What I like at Canon: Being able to speak your mind without worrying about hierarchy
Time off: I enjoy spending time with my family
The cloud is now more convenient than ever.
Kenta InoueGen3 models feature uniFLOW Online, a function extension platform that provides a range of services by integrating the MFDs and the cloud. There’s an array of features that contribute to improved workflows—including user authentication, report generation leveraging usage data management, sending scan data from the MFD directly to external storage services, printing to other cloud-connected MFDs, and mobile print.
uniFLOW Online
-
- Send directly to the cloud
-
- Print anywhere
People think MFDs have rich features but difficult to use.
InoueNo matter how good your service is, nobody will use it if it's not user-friendly. We’ve just launched uniFLOW Online, but we believe what’s most important is ensuring everyone feels that they can easily take advantage of its excellent functionality; to feel that it’s really convenient. When we were putting the service together, we aimed to put all the complexity and advanced features in the cloud and enable users to take advantage of them with a touch of a button. We made sure that setup after installation could be completed in simple steps on the MFD, reducing hassle as much as possible from account creation to connecting the device to a network.
Is there a reason for having these services in the cloud?
InoueCloud services such as uniFLOW Online provides easy access to functions not available on the MFDs such as handling jobs that require much processing power and making use of systems that would be otherwise difficult to implement simply by connecting to the cloud. In addition, if the MFDs are connected to the same cloud, those MFDs can perform the same function wherever they are located.
For example, say you have a lot of receipts. Scanning them one by one would be quite cumbersome, but with uniFLOW Online, you can have multiple receipts on the scanned and with just one scan pass, each receipt can be recognized individually and processed as separate receipts. MFDs connected to the same cloud can access this service from any location.
If users feel their work efficiency has improved with the cloud, I believe the resistance to using cloud services will fall away and more people will feel comfortable using them, leading to cloud services growing and work styles changing.
I believe you co-developed uniFLOW Online with a German company. Is that right?
InoueThe original software for uniFLOW Online was created by NT-ware, a Canon Group company in Germany, and we worked together with them to develop it further and expand the platform's functionality. It was a challenge because of the culture and way of thinking are different to what we're used to in Japan. For example in Germany, people generally don’t mind reading such long documents as instruction manuals, so control screens tend to show text explanations, but in Japan, people prefer graphical information, so screens with icons and images are considered easier to understand. When we had differences of opinion, we both referred back to our concept—customers should be able to use things in a simple manner—and after repeated discussions, would find a solution.
Collaborating closely with our colleagues overseas was very rewarding. I myself am still not that fluent in English, but I’m enthusiastic about using a chat system to communicate. I’m sure there might be opportunities to work in Germany in the future, so I’m looking forward to that."
Cloud integration has made things quite exciting, hasn't it?
InoueWhen you talk about office multifunction devices, most people just think of it as a photocopier or a printer, but it was really interesting actually being involved in the development of one, because I realized that they are full of different technologies—mechanical, chemical, electrical, operating system software, firmware, the cloud, security and more. It was so rewarding to work with experts from all kinds of technological fields toward solving our customers’ issues and seeing them enjoy the added convenience. It was also fun to see my own specialist knowledge directly benefiting the customer.
"The rapid pace of MFD evolution is mind-boggling, with new devices coming along as the office environment changes. We now know the engineers continue to work each day to figure out how to respond to changing work styles and their new requirements, while searching for ways to increase convenience and comfort.
These engineers derive satisfaction as professionals while working shoulder to shoulder as a team, relying on a common concept to break through differences of opinion and position. We can’t wait to see what else this ""multifunction"" team comes up with in the future."
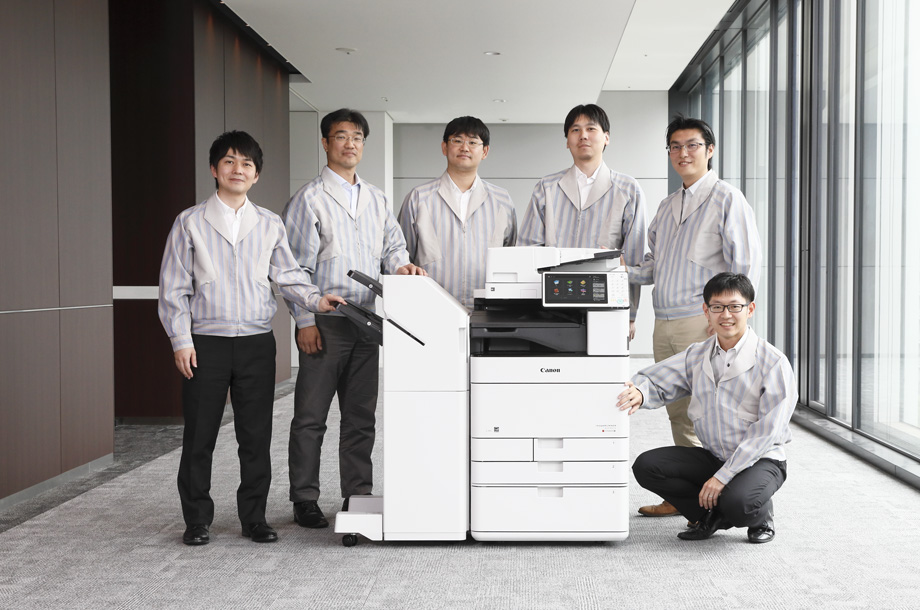