Shaped by photo printing, brought to the world of commercial prints
Print Image Quality Quantitative Evaluation Technology
Through development of evaluation and simulation technologies that can quantify how a person would feel about the quality of an image, Canon has successfully produced high-speed digital presses capable of high image quality. This broadens their possibilities in graphic arts printing.
April 27, 2023
Print quality: The problem that held back the digital transformation in commercial printing
Businesses across all industries are rapidly pursuing digital transformation. Commercial printing, which includes catalogs, books, magazines, tickets and direct mail, is no exception.
The most widely used printing method is offset printing, an analog method that involves the transfer of ink from a metal printing plate to the printing surface via a rubber blanket. It achieves consistently high printing quality, which makes it well suited for making high-volume prints of the same content.
On the other hand, the up-and-coming method is digital printing, where an image based in digital data is printed directly onto the printing surface. As printing plates are not required, this method is more suitable for variable printing for materials such as direct mail and bills, where on-sheet content may differ for every page, and print-on-demand (POD) printing, which produces fewer copies per run.
Amid the growing trend towards “paperless offices”, organizations are printing less. When they do print, they do so with greater variety but in smaller quantities. Digital printing, which caters to this need, therefore continues to grow.
One of the issues facing the digital transformation away from offset printing was that high-speed printing usually compromised print quality. Using inkjet presses to print digitally enabled printing speeds that matched offset presses, but at the expense of output quality. This made it difficult to use digital presses for photographs, catalogs, and other types of graphic art printing, where image quality is extremely important.
To achieve the high image quality that would attract users of graphic art printing, Canon established its Image Quality Quantitative (IQQ) Evaluation technology.
Digital printing caters to the demand for a larger variety of prints in smaller quantities.
Quantifying image quality evaluation
When a new production press system is being developed, image quality evaluations are conducted at various stages of the development process. Traditionally, this evaluation was assessed through subjective means, i.e., based on a person’s perception of image quality. Acceptable ranges and opinions on image quality differ from person to person, and therefore it was difficult but essential to obtain reliable evaluation outcomes.
As the pioneer of two major digital printing processes that it had developed from scratch—the electrophotographic process in the 1960s, and the inkjet printing process in the 1970s, Canon had realized very early on the need to establish a suitable technology for image quality evaluation, as this would be the foundation for future development. Therefore, the company began to develop such technology.
The plan was to develop a system that would assign a value to (i.e., quantify) criteria, replacing the current subjective evaluation system. Canon began to compile knowhow on evaluation benchmarks and processes, ranging from photo quality evaluation—cultivated over the company’s decades-long history—to knowledge it had gained from developing digital photo printers, inkjet printers, and cameras and lenses. From these, it distilled human perception of image quality into five factors, which it set as evaluation metrics. These are:
- Noise (banding and graininess)
- Text and lines
- Sharpness
- Color
- Gloss
Next, they created charts that showed simple descriptions of evaluation metrics and, based on these charts, conducted subjective evaluation. For each metric, they obtained reliable subjective evaluation values with consistent focus areas and standards.
In addition, the development team measured the correlation between human visual characteristics and the characteristics read by meters such as high-definition scanners and colorimeters. These results were used to devise a conversion method that could correlate the scanner-measured value to a subjective evaluation value for each metric. Thus, the “human perception of image quality” could now be quantified using the measured scores for an image. This technology enabled image quality evaluation to be performed objectively anywhere in the world.
Canon’s inkjet presses are particularly well-suited to variable printing, which includes business forms and bills. They are developed and manufactured by Canon Production Printing (CPP), which operates in the Netherlands and Germany. Europe-based CPP and Japan-based Canon work closely together to develop high-speed inkjet presses that can handle graphic art printing, with IQQ evaluation as their common language.
The 5 IQQ evaluation metrics
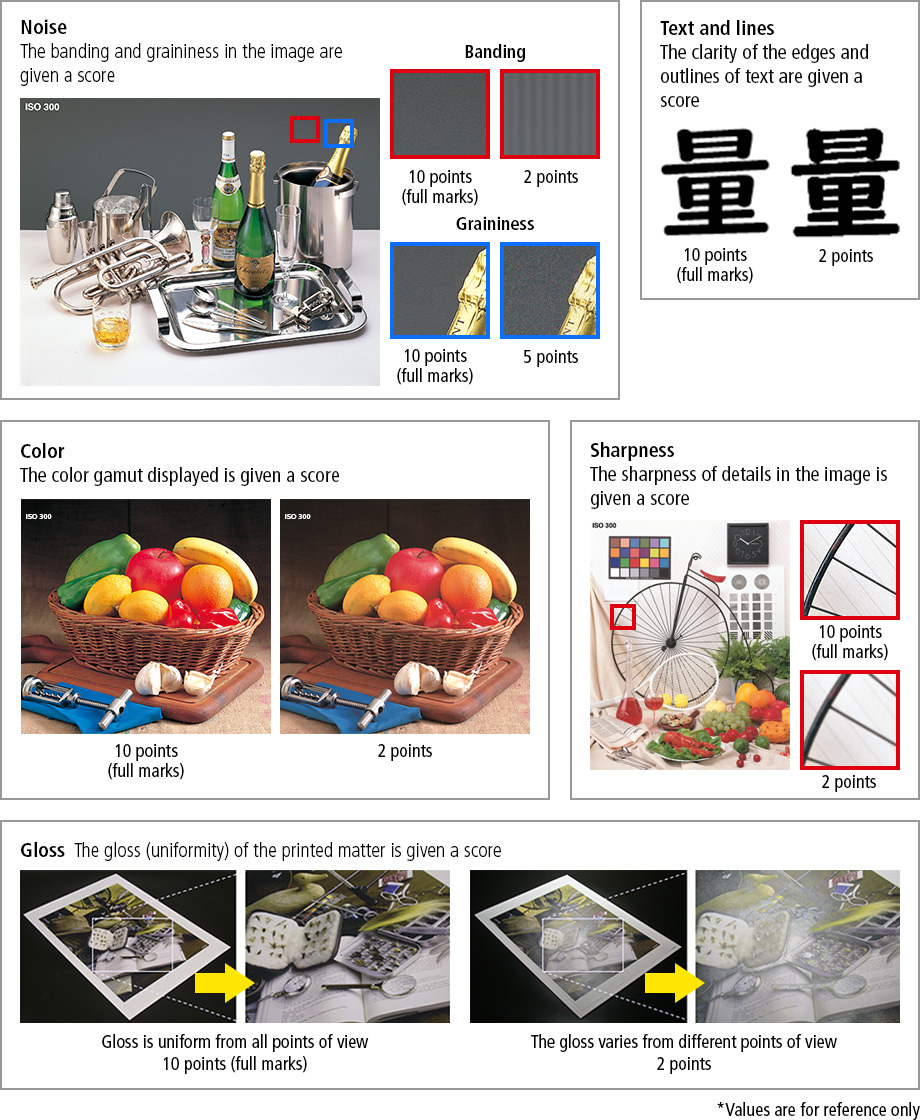
Image processing: The solution to the banding and noise that plagued high-speed inkjet printing
Production print systems are expected to print at high speed, employing the linehead method of printing which involves ink nozzles lined up across a horizontal printhead. This method is prone to banding, which may occur due to nozzle blockages or slight differences in ink consistency between nozzles.
One method of making banding less obvious is to intentionally incorporate noise grains into the image and then blur them. However, this could make the resulting output appear grainy depending on the method used. Banding and graininess cause graphic arts projects such as photography collections and catalogues to diminish in value as commercial publications.
Banding and graininess have a trade-off relationship, which needs to be in perfect balance to deliver the high image quality demanded by graphic arts commercial printing. The issue was solved by Canon’s advanced image processing technology for inkjet presses, with IQQ evaluation employed to check and verify outcomes throughout the process.
Before printing, a nozzle check pattern is printed to detect and assess banding. The line sensors located immediately behind the printhead check the status of each ink nozzle by reading and analyzing the lines in the pattern.
Based on the results of the scan, the system corrects the ink output to reduce the visibility of banding. It tops up the ink in nozzles if the ink is too thin, and reduces the ink in nozzles if the ink is too thick. The nozzles to the left and right of any blocked nozzles are used to compensate them .
A nozzle check pattern is also regularly printed during the printing process, which ensures high image quality with no banding throughout the entire job.
Canon’s technology ensures high image quality with no banding (varioPRINT iX series)
On the other hand, the parameters (dot array patterns) for graininess reduction processing are usually set before the product is delivered to the market. The parameters assume that the volume of ink in the nozzles are uniform. However, in reality, the volume of ink in each nozzle is adjusted to correct banding, so a new array intended to correct graininess would upset the adjustments, and may even introduce other forms of graininess.
To counter this, Canon developed new parameters. The company used IQQ evaluation technology to ensure that the design-development-evaluation cycle progressed efficiently, thus achieving stable, high image quality with neither banding nor graininess—a feat that was once difficult to achieve with high-speed inkjet printing.
Catering to the diverse needs of the graphic arts genre
The varioPRINT iX series of high-speed sheetfed inkjet digital presses was jointly commercialized by Canon and CPP. Compared to its predecessors, it boasts dramatically improved photo and graphic arts image quality. Many new orders have been placed for these digital press models from businesses in the graphic arts market. In 2021, the series won the BLI Outstanding Innovation Award in Production Print, presented by Keypoint Intelligence, a globally influential independent evaluation body based in the United States. Catering to the graphic art printing industry’s needs for varied printing in small quantities is just the beginning. Canon will continue to serve a diverse range of needs as it seeks to further expand the market for digital presses.
IQQ evaluation technology sets evaluation values based on measured outcomes from print products. In doing so, it enables reliable image quality evaluation to be conducted anywhere in the world. Many more applications for this technology are expected to emerge on the global stage, including in the quality improvement sector.
varioPRINT iX series