-
New industry-oriented business group structure: Printing Group
Instantly. Beautifully. Securely. Anywhere. Digital printing is growing and supporting today's wide range of printing needs.LEARN MORE
-
New industry-oriented business group structure: Medical Group
"No medical care without diagnostics." Improving care together with patients and healthcare professionals.LEARN MORE
-
New industry-oriented business group structure: Imaging Group
Imaging is vital to future society. Canon's technology creates new possibilities for enriched lives in a new era.LEARN MORE
-
New industry-oriented business group structure: Industrial Group
By supporting semiconductor and display production with super-precision technology, Canon contributes to the advancement of digital societyLEARN MORE
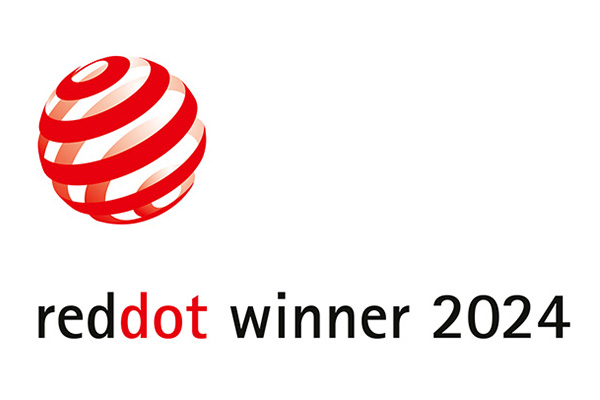
April 26, 2024
"PowerShot V10" vlog camera and "OCT-R1" ophthalmic device win international design award "Red Dot Design Award"
JAPAN
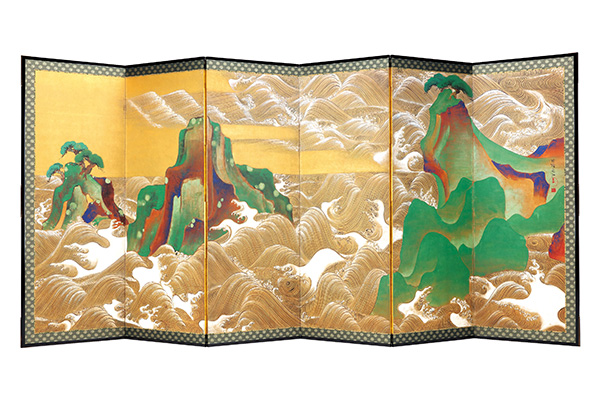
April 25, 2024
Tsuzuri Project donates to Kyoto City University of Arts a high-resolution facsimile of Ogata Kōrin's "Waves at Matsushima," to be displayed at an area of the university open to the public
JAPAN
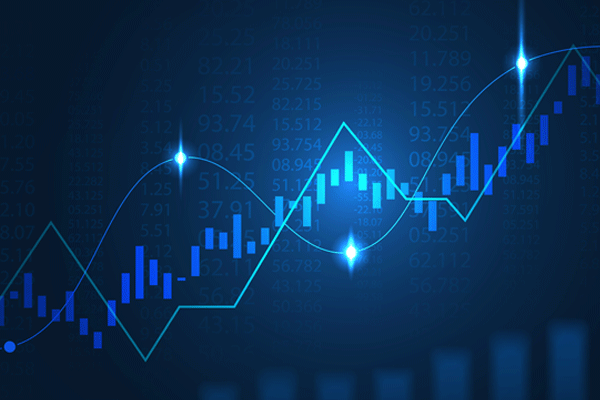
April 24, 2024
Canon releases results for 1Q 2024
JAPAN
MORE CONTENTS
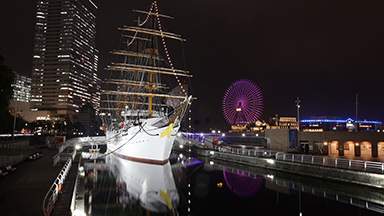
Commitment to Quality
Great progress is being made to eliminate camera shake in both bodies and lenses, enabling anyone to take clear pictures with hand-held shooting.
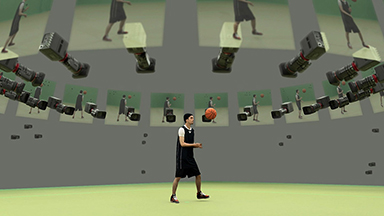
Volumetric Video Technology
Volumetric video is a technology which reconstructs a 3D space data from captured images. This video introduces the basic principles of the technology.
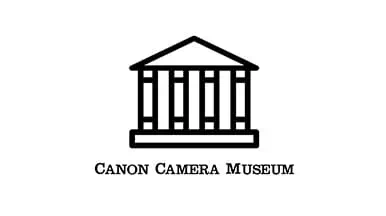
Canon Camera Museum
Canon Camera Museum provides historical information, such as the history of Canon and descriptions about all cameras and lenses released since it was founded.
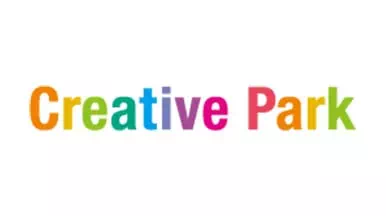
Canon Creative Park
You can download fashionable cards and fun paper craft for free. Enjoy everything right away with an inkjet printer and paper.
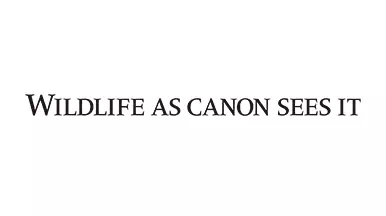
WILDLIFE AS CANON SEES IT
You can find advertisements featured in National Geographic until 2020.