Safety Program
Canon’s Approach to Safety
In-house standards for greater safety
At Canon, we believe that the most basic and important duty of a manufacturer is to provide its customers with products and services that are 100% safe. In order to make this possible, we require that all Canon products comply with safety standards already established by law as well as our own Substantial Safety1 standards devised from our customers’ perspective.
For example, we employ plastics that are more flame resistant than the law requires, and we implement redundancy protections for important safety-related components. Such company standards that incorporate enhanced safety measures are mandatory throughout the Canon Group and strict checks are enforced during every step of the manufacturing process to make sure they are adhered to. In addition, we continue to examine and reevaluate our safety standards in response to such changes as advances in technology or new ways that customers use our products.
- 1 Substantial safety: Safety not only in terms of what is required by laws and statutes, but any safety issue that can reasonably be expected to arise during customer use.
Facilities and Measures for Testing Safety
Testing to Evaluate and Confirm High Safety Standards of Facilities
Canon Inc. has set up testing facilities compliant with public standards and relevant laws to accurately and thoroughly assess the safety of products in terms of electromagnetic interference (EMI), noise, flame resistance ratings, volatile organic compounds (VOCs), and genotoxicity. Canon has also obtained certification in public standards such as ISO1, IEC2 and OECD3 from domestic and international organizations, enabling certified testing to be carried out in-house according to highly precise measurements, as well as testing and verifications that are stricter than these standards.
- 1 International Organization for Commission
- 2 International Electrotechnical Commission
- 3 Organization for Economic Co-operation and Development
Pick Up
Test Facilities and Safety Evaluation
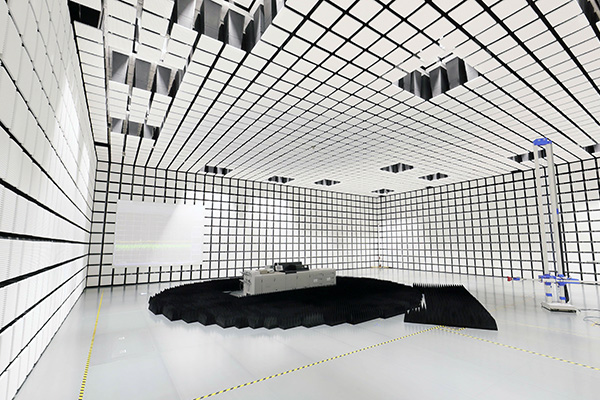
Electromagnetic emissions: Canon possesses industry's leading scale anechoic chambers and shielded rooms, which are used to determine whether unnecessary electromagnetic waves emitted by products affect other products and whether products will malfunction due to the effects of lightning, TV electromagnetic waves and other interferences.
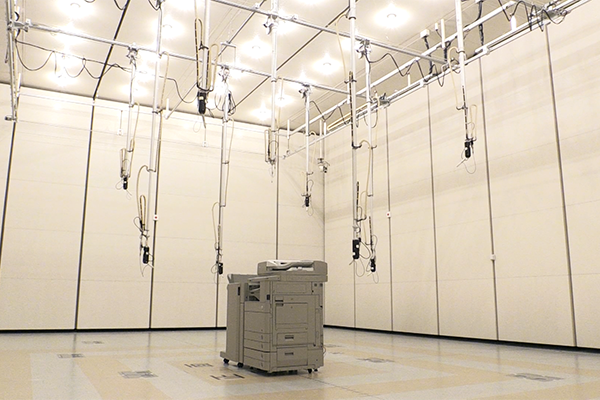
Noise: Canon has established a hemi-anechoic room with sound-absorbing materials installed on the walls and ceiling, leaving only the floor, to evaluate the various levels of noise produced by products via measurements based on ISO/IEC 17025 standards. Testing is also performed for extremely quite noises measuring.
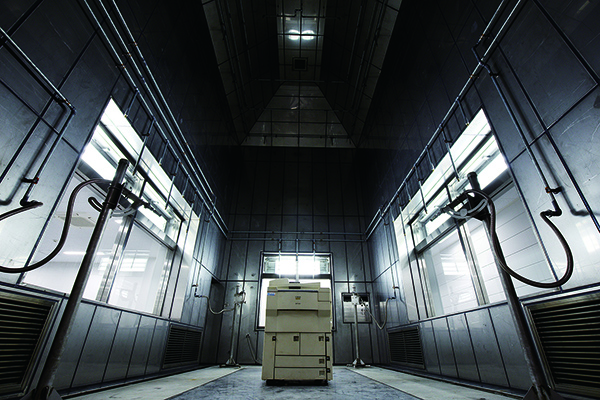
Flame resistance: Along with testing for large products in a large-scale flame resistance verification room, Canon possesses a plastic flame resistance testing room in which flame resistance evaluation is performed for plastics including product covering.
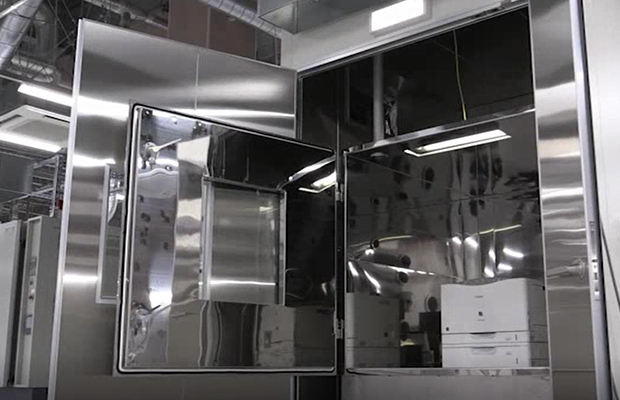
Chemical substances released from products: Canon assesses the chemical emissions from its printers, multifunctional devices (MFDs), projectors, and other products. We also measure volatile organic compounds (VOCs) for which exposure limits have been set both within Japan and internationally, verifying that emission levels meet our in-house standards, which match or even exceed those set worldwide.
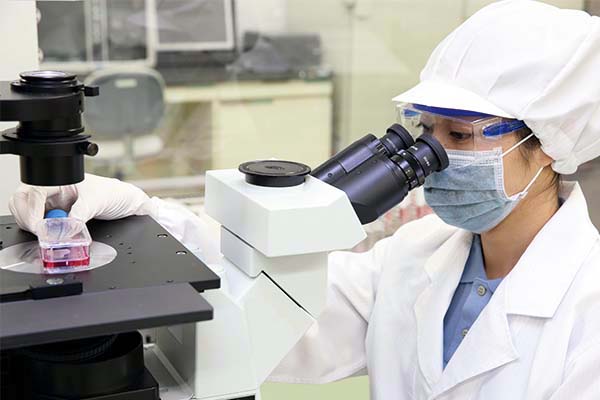
Ink, Toner and Other Consumables: With regard to the materials for ink and toner, we carry out assessments related to genotoxicity, thought to be closely linked to carcinogenicity, using bacterial reverse mutation tests and in vitro mammalian cell micronucleus tests. Canon’s testing laboratories are highly reliable and have been certified by Japan’s Ministry of Health, Labour and Welfare as in compliance with Good Laboratory Practice (GLP) standards. Canon’s laboratories also comply with GLP standards set by the Organization for Economic Cooperation and Development (OECD). Furthermore, Canon became the first in Japan to have its in vitro mammalian cell micronucleus test certified as in compliance with the GLP standards in the Chemical Substances Control Law.
- 1.Facilities supporting ISO and IEC testing: large-scale anechoic chambers, shielded rooms, hemi-anechoic chambers
- 2.Facilities supporting EMC testing: large-scale anechoic chambers, shielded rooms, hemi-anechoic chambers
- 3.Facilities that support testing required for acquisition of Blue Angel environmental labeling certification: large-scale anechoic chambers, shielded rooms, hemi-anechoic chambers, special-purpose chamber for chemical substance emission testing
Ensure Safety and Reliability of Electrical Components
Canon considers it essential to maintain and improve the quality and reliability of every component, including semiconductors and various electric parts, to ensure products are safe and reliable. We have developed and continue to strictly implement our own in-house quality certification system for electric parts. When selecting parts under this system, we evaluate reliability and structural soundness in accordance with standards for each type of part, ultimately using only electric parts that meet these standards of quality. Moreover, to make structural evaluations at the selection stage and scan for defects, we utilize high-precision nondestructive evaluation technologies, such as X-ray CT scans and thermal analysis, as well as detailed processing, observation, and measurement.
Note:
Additional information based on Canon's Basic Policy on Product Safety, including our Voluntary Action Plan, After-Sales Support, Responding to Product Quality Issues and Process for Responding to Quality Issues, can be found on the “Product Responsibility” page of our CSR Activities site.
https://global.canon/en/csr/people-and-society/product/index.html
List of Content
Maintaining Trust in the Canon Brand
Vol.10
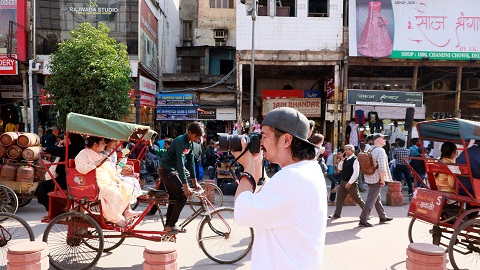
Vol.9
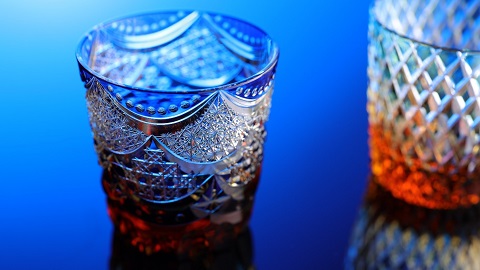
Vol.8
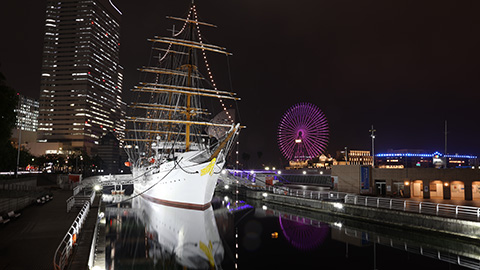
Vol.7
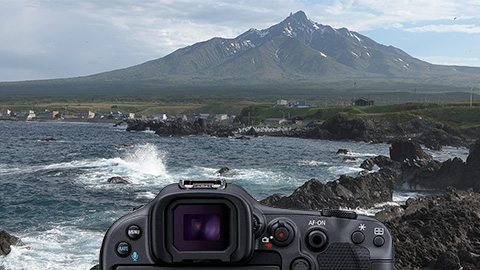
Vol.6
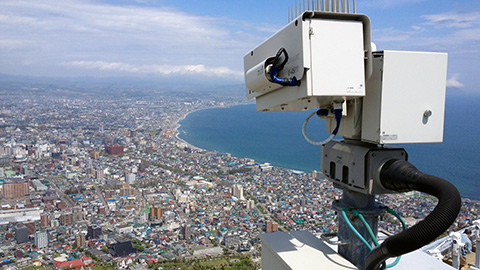
Vol.5
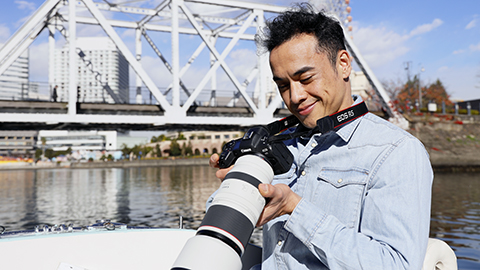
Vol.4
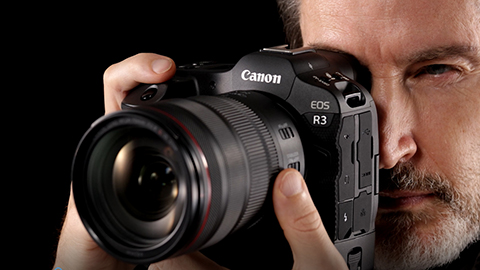
Vol.3
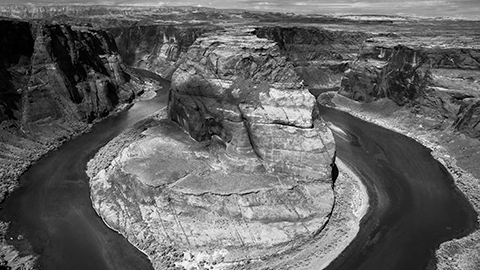
Vol.2
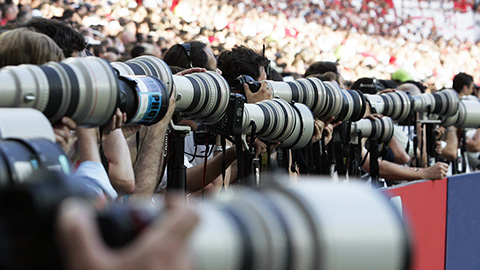
Vol.1
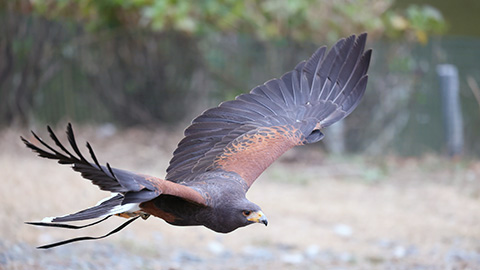
Canon QA Activities
Quality Management at Canon
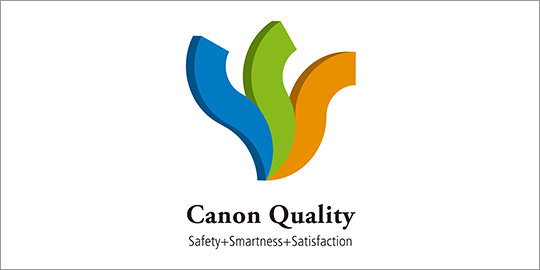
Safety Program
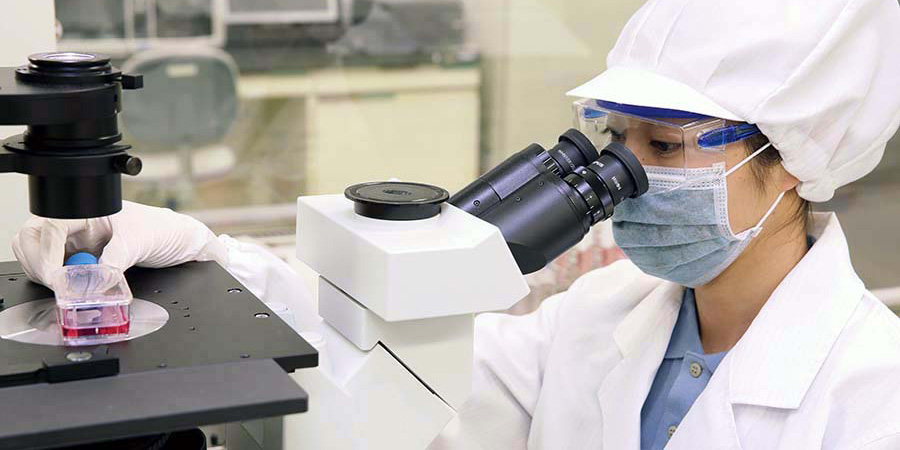
Security Measures
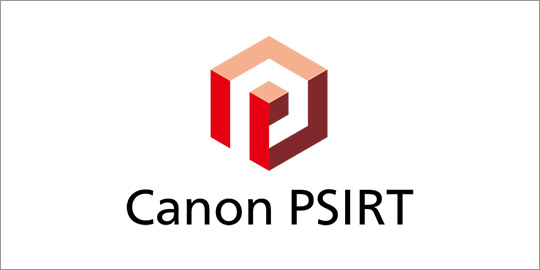