5,000 lines, yet as thin as a human hair!
Imprinting: the future of semiconductor lithography
Next-generation semiconductor microfabrication technologyThe Story Behind Nanoimprint Lithography
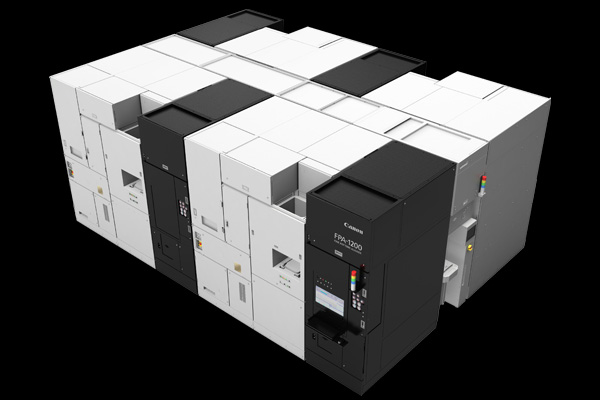
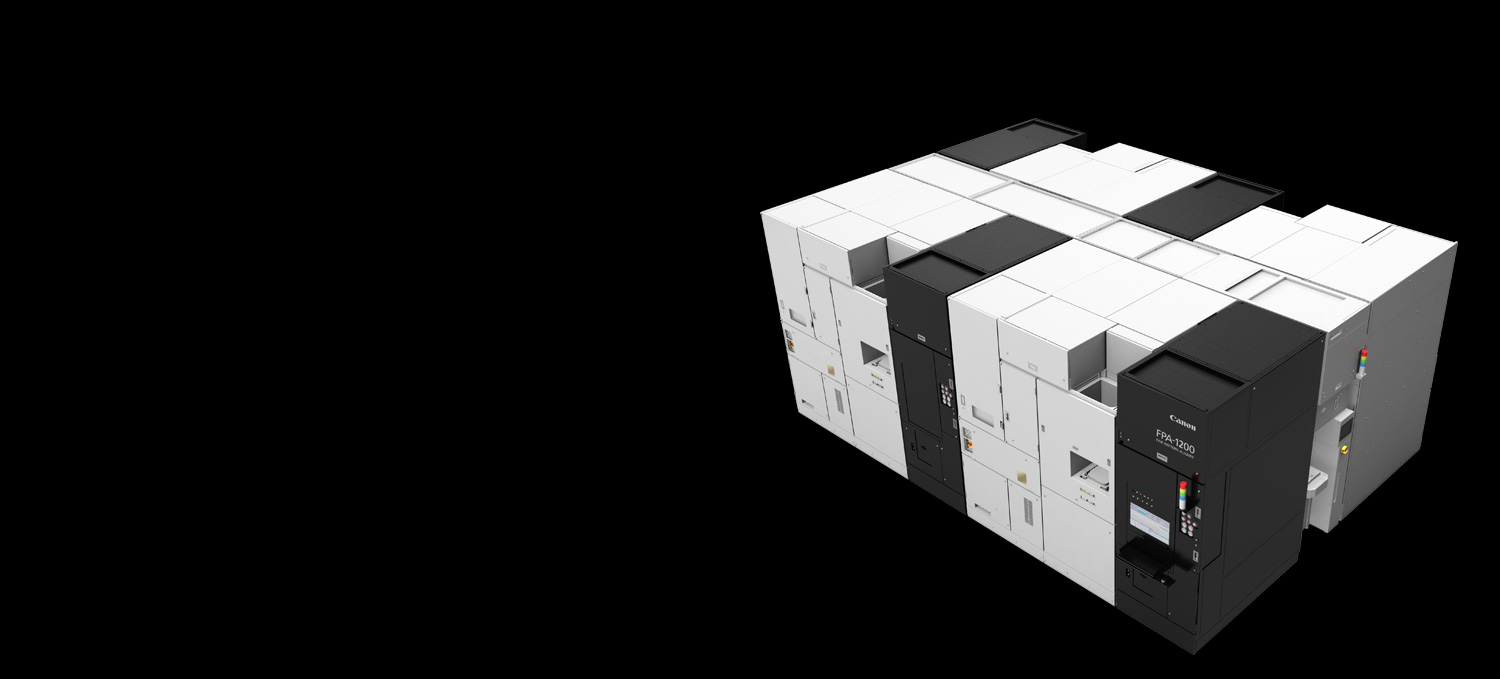