Technology in ProductsOrganic Light Emitting Diode (OLED) Display Manufacturing Equipment
Equipment that produces next-generation displays that are thin, lightweight, vivid, and high-definition
Devices such as smartphones, televisions, and personal computers are becoming thinner and lighter, while offering higher image quality. Facilitating this advancement are OLED displays that are thin, lightweight, and produce vivid colors. OLED display manufacturing equipment is used to manufacture high-definition OLED displays through the process of layering organic materials on glass plates with precise positioning.
June 8, 2023
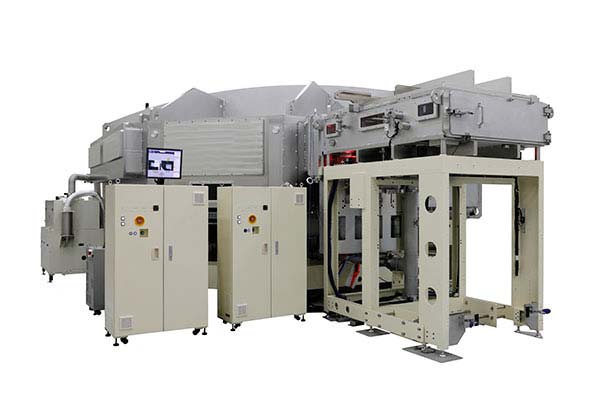
How OLED display manufacturing equipment works
What is an OLED display?
The images shown on the displays of smartphones and televisions that we use in our everyday lives consist of fine dots that glow red, green, or blue, as illustrated by this figure. Displays can be divided into two types depending on the way these dots are illuminated. Liquid crystal displays (LCDs) produce colors by shining light from behind a red, green, or blue color filter, and OLED displays use organic materials that emit light on their own.
Read More
Technologies in OLED display manufacturing equipment
Deposition technology
Deposition is the process of forming a very thin film on a glass substrate using organic materials. In the manufacture of OLED displays, this is done through the “vapor deposition process.” A high vacuum is maintained in the chamber. An evaporation source (a crucible) is packed with an organic material and heated to approximately 300°C, and the material is evaporated. Evaporated particles issuing from the evaporation source travel in a straight line and adhere to the glass substrate with almost no collisions between the particles.
A monitor that uses a quartz plate as a sensor (hereafter, “quartz crystal monitor”) plays a major role in this step. A quartz crystal monitor is used to control the vapor deposition rate. The speed at which evaporated particles move toward the glass substrate is detected by the quartz crystal monitor and is kept constant. Evaporation is terminated when the specified film thickness is achieved. In order to adjust the level of coloration of a light-emitting material during vapor deposition, a certain percent of a different material must be added. To maintain a constant percentage of that material, Canon uses a quartz crystal monitor to precisely control the vapor deposition rate.
In order to consistently mass-produce displays of the same quality, each organic material must be consistently deposited over a long period of time. Canon's deposition technology utilizes quartz crystal monitors, thus enabling consistent deposition over long periods of time and facilitating the manufacture of displays that can produce vivid colors.
Alignment technology
The vapor deposition process for OLEDs involves the coating (patterning) of a light-emitting materialwith each color (red, green, or blue) simultaneously with vapor deposition. Organic materials cannot be patterned by etching (surface processing) after deposition because thin films of those materials can be damaged. Therefore, patterning must be performed at the same time as vapor deposition. The method used in this process is to place a vapor deposition mask (a metal plate with holes) opposite the glass substrate to deposit a material emitting red, blue, or green light in the desired position in accordance with the mask pattern. First, a vapor deposition mask for red is used so that the color is applied only to the areas where red is to be vapor-deposited. Afterwards, a vapor deposition mask for green and then blue is used so that each color is applied in the appropriate place.
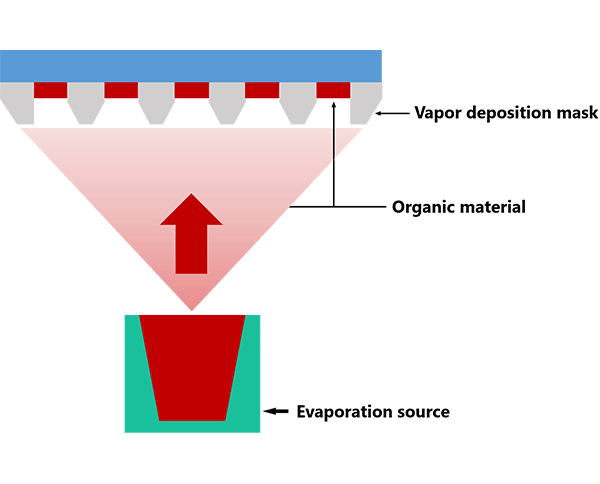
Evaporated organic material adheres to the exact location through the vapor deposition mask
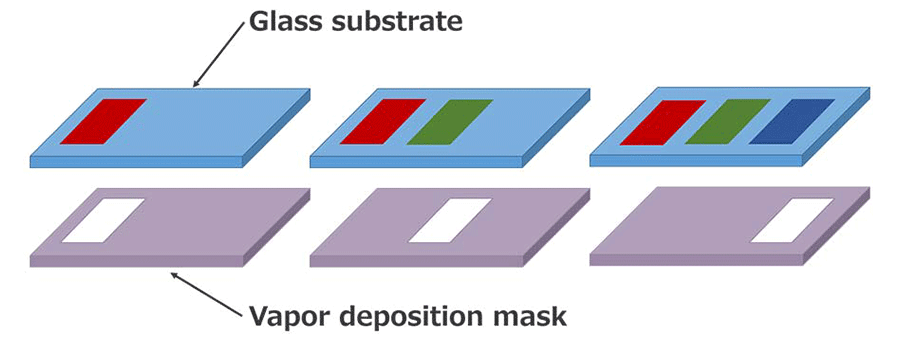
Use of a vapor deposition mask for each color to coat the substrate with red, green, and blue in specific places
Positional information is acquired with a camera and highly precise alignment is performed
The manufacture of OLED displays with higher definition and resolution requires the vapor deposition of light-emitting materials in precise positions. Therefore, alignment (placement) technology is required to precisely align the vapor deposition mask with the glass substrate. Alignment is performed by acquiring positional information for the vapor deposition mask and the glass substrate by means of a camera and then precisely controlling the positional relationship between the mask and substrate.
In recent years, the resolution of smartphones and televisions has continued to increase, and there is a growing trend to increase resolution to 4K or 8K. Canon uses this alignment technology to achieve highly precise positioning and thereby meet the growing demand for higher resolution and higher definition displays.