Technology in ProductsFPD Lithography Equipment
Manufacturing Equipment Vital for the Production of
Liquid Crystal, OLED, and Other Displays
Flat panel displays (FPDs) are essential for displaying images on televisions, smartphones, digital signage, and other display devices. FPD lithography equipment is critical to display manufacturing and formation of submicron pixel circuits on glass substrates. FPD manufacturing requires advanced optical technologies and high-precision, high-speed alignment capabilities and FPD lithography equipment plays an important role that is directly tied to substrate quality, yield and production efficiency.
December 2, 2021
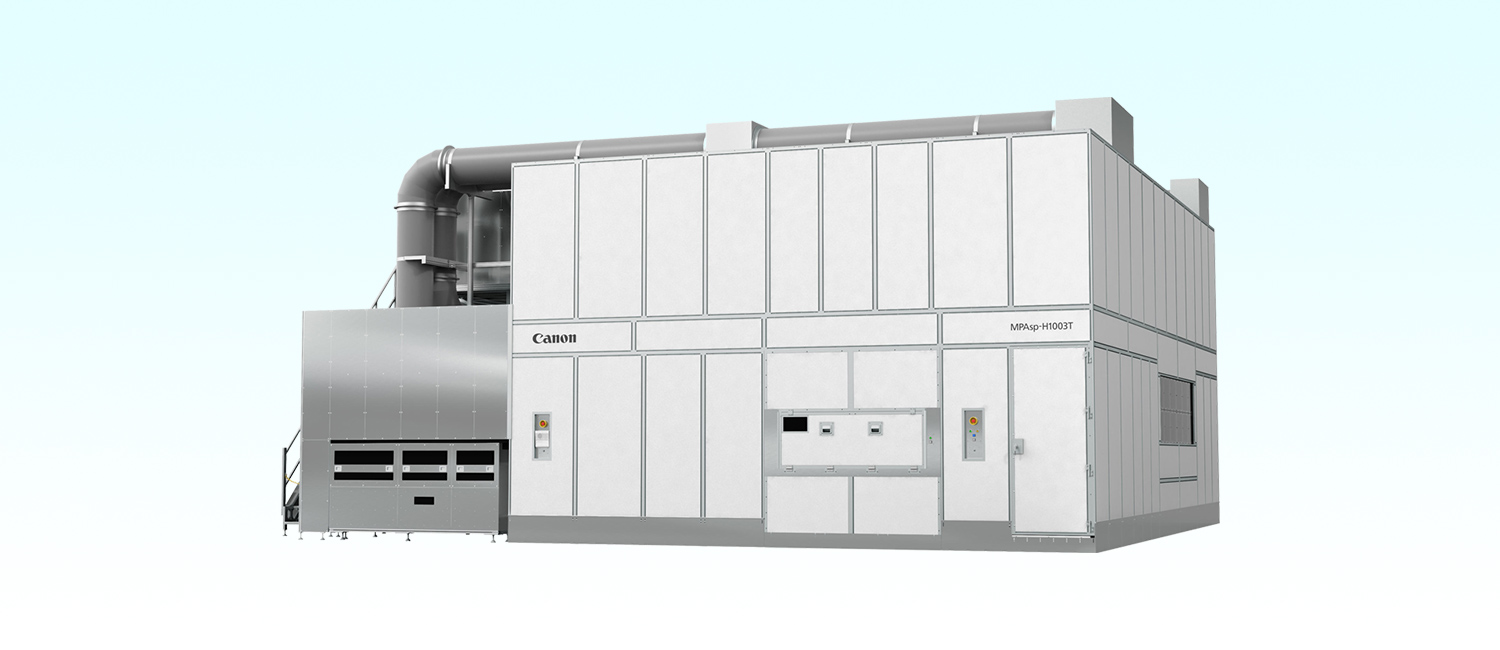
How Flat Panel Display (FPD) Lithography Equipment Works
"Flat panel display," or "FPD," is the collective term for display technologies including liquid crystal displays and organic light emitting diode (OLED) displays. FPDs of various sizes are used in many display devices you encounter everyday including televisions, computers and smartphones.
Read More
Canon Lithography Technology
Canon is a top manufacturer of high-resolution lithography equipment that is vital for FPD fabrication. As part of the photolithography process Canon's FPD lithography equipment uses a mirror-projection method that performs exposure using a reflective optical system with a large, high-precision concave mirror at its core. The mirror is large enough to expose large displays in a single exposure to produce seamless, high-precision panels.

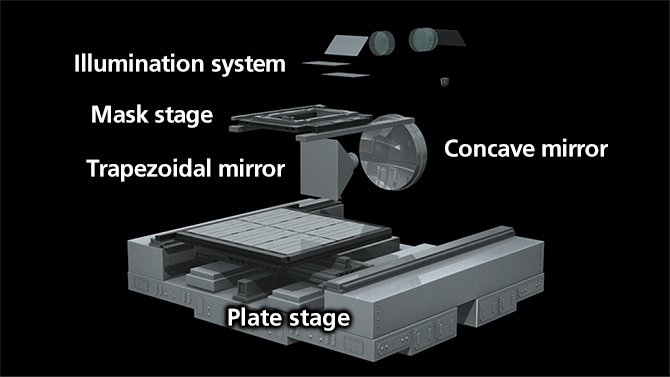
Optical Technology for Single Exposure of Large Displays
Large, Ultra-Precise Concave Mirror Projector
Photolithography process requirements range from small area exposure of semiconductor IC chips to very large single-exposure of liquid crystal and OLED displays. In 1980, Canon developed its first Mirror Projection Aligner (MPA) lithography equipment supporting to support a variety of photolithography applications.
MPA equipment integrate a large concave mirror (projector), small convex mirror and trapezoidal mirror that have all been created using the highest possible machining precision.
The photomask mounted on the MPA photomask stage is illuminated with intense ultraviolet light that is reflected five times to accurately transfer the circuit pattern from the photomask to the photoresist on the glass substrate via exposure.
The concave projector mirror is the key to transferring the micron-order circuit patterns to large glass substrates. The roughly 1.5 meter diameter concave mirror projector stands out from the competition and is made possible by Canon precision optical and production technologies.
MPA lithography equipment is completely optically symmetrical which offers two fundamental advantages. Mirror projection systems suffer no comatic aberration that can occur when light enters a medium at an angle. MPA optical systems also have no chromatic aberration that can occur as a result of differences in light wavelength and is a potential problem for refractive optical systems employing lenses.
An arc-shaped exposure area produces the best possible image-formation characteristics and the equipment scans an arc-shaped exposure area to achieve high-resolution performance over a large area.
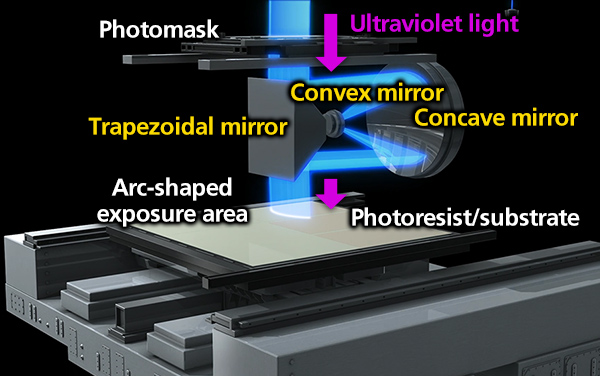
Illumination System with Large-Area Uniformity and High-Intensity
Uniform, Bright Illumination
There is an ongoing need to shorten FPD lithography equipment tact time to increase productivity. Canon photolithography technology utilizes an ultraviolet light illumination system with increased illumination intensity to transfer photomask patterns onto photoresist via exposure. Higher intensity reduces exposure time and greatly shortens tact time which contributes to greater productivity for panel manufacturers.
MPA also benefits from employing a mirror projection optical system having no chromatic aberration.
The system leverages this advantage to increase illumination intensity by effectively utilizing ultraviolet light over a wide wavelength range (i-line: 365 nm to g-line: 436 nm) without sacrificing resolution performance.
MPA equipment also support finer resolution device fabrication using even shorter wavelengths (DUV wavelength: 290 nm to 380 nm).
MPA equipment also combines three high-output ultraviolet lamps to further increase illumination intensity.
However, increasing illumination intensity by simply adding more ultraviolet lamps can lead to uneven illumination which will degrade resolution performance. To allow combination of 3 ultraviolet lamps, Canon developed optical technologies including a fly’s-eye lens and precise adjustment techniques by complementary optical systems to achieve uniform and high-intensity illumination.
Hybrid Alignment Technology
Fast, Accurate Measurement and Shortened Tact Time
Canon FPD lithography equipment shortens tact time by increasing drive speed of stage that holds the display plate. Another method for reducing tact time is to use two different types of alignment mechanisms to reduce alignment measurement time.
One issue faced when developing high-speed alignment measurement technologies is that when a glass substrate undergoes processes such as heat treatment, the substrate's absolute dimensions may change. This results in various distortions in the coordinates of the pattern formed during the previous process. To accurately assess this distortion, it is necessary to measure numerous reference-point positions.
Alignment measurement has conventionally been performed using the (AS) method that uses the actual mirror optical system light paths to measure the overlap between the alignment marks on the photomask and the substrate.
Canon has also introduced a new measurement system called off-axis scope (OAS) without using the exposure light paths in which alignment marks are directly observed on the substrate, after which indirect alignment is performed. Canon's "Hybrid Alignment System" uses both of these methods simultaneously to assess distortion, making it possible to both reduce tact time and improve measurement accuracy.
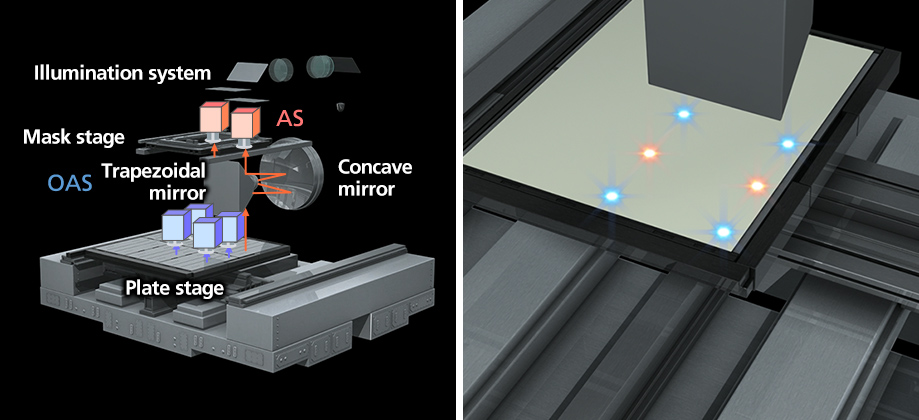
Long Stroke, High-Precision, High-Speed Stage
Rapid Movement of Objects as Heavy as Small Trucks with Meter/Second-Order Speeds & Submicron-Level Precision
Shortening tact time also requires a long-stroke, high-speed plate stage, however, plate stages that support glass substrates with large surface areas are very heavy. The X-direction stage, which is as heavy as a compact car, and the Y-direction stage beneath that can weigh as much as a small truck must be moved quickly and accurately.
Canon uses laser interferometer-based ultra-precise, nanometer-level measurement, powerful linear motors, and air-bearing technologies to achieve long-stroke, high-speed and high-precision control of the movement of these large stages.
These technologies have made it possible to achieve meter-order strokes with sub-micron-level positioning precision and reduced tact time through high-speed stage movement.
Canon equipment also incorporates calibration technology that makes fine adjustments to the plate stage scanning speed and scanning direction during exposure. Scan exposure correction can help correct photomask patterns to match for distortions in the pattern on the substrate that may result from upstream process steps such as heat treatment or etching. Scan exposure compensation improves both accuracy and productivity.
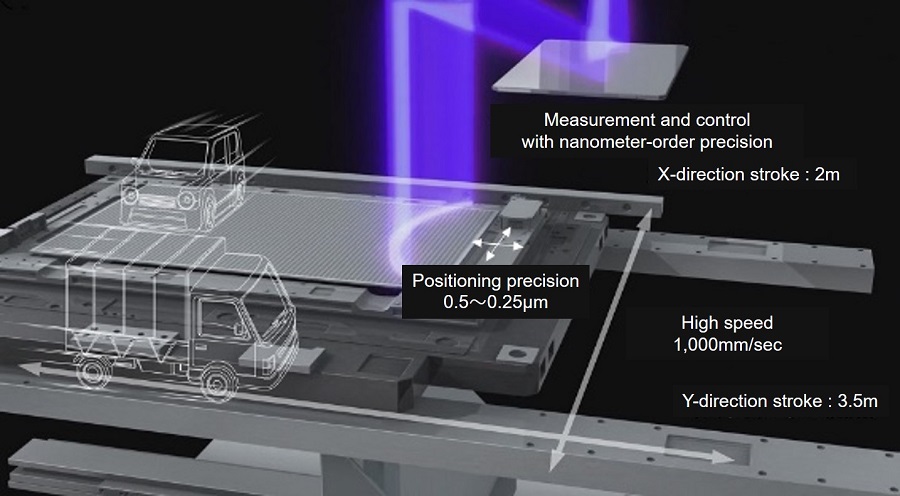
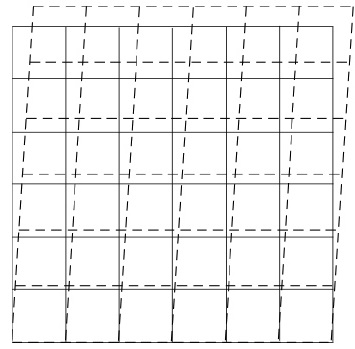
Canon technology compensates for pattern distortion resulting from previous processes. By performing fine adjustments to scan speed and direction during exposure, MPA equipment can accurately align photomask patterns and overlay existing patterns.
Nonlinear Distortion Correction Technology Corrects for Distorted Patterns
The absolute dimensions of glass substrates with large surface areas may change as the panel undergoes heat treatment or is otherwise affected during processing. Panel distortion must be addressed to allow a pattern from a distortion-free photomask to accurately overlay a pattern on a distorted panel. To correct for panel distortion, Canon FPD lithography systems incorporate not only a scanning-correction mechanism for making fine stage-driving adjustments, but also independent X and Y-direction magnification-correction mechanisms for correcting nonlinear distortion that cannot be completely resolved by scan drive correction alone. The system can dynamically adjust the exposure light path in the X and Y directions during stage scanning to enlarge or reduce the projected pattern. MPA equipment can apply magnification technology in conjunction with scanning-correction mechanisms to correct for various distortion shapes on the substrate and to more accurately match the photomask pattern to the pattern on the panel.
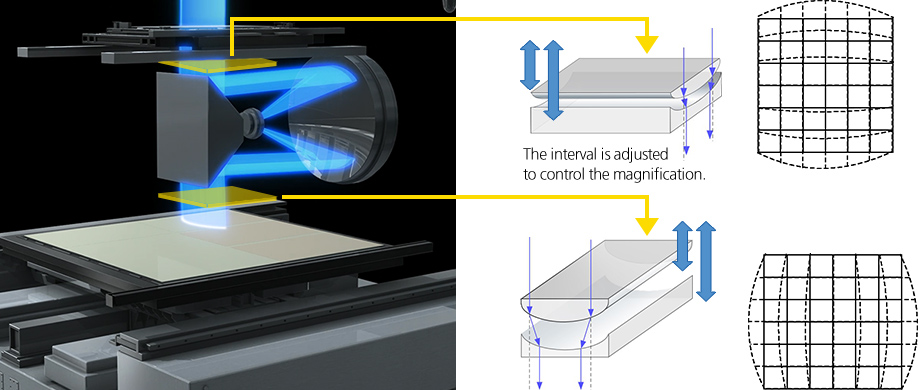