About Canon

Corporate Profile


Corporate Profile Updates
- April 1, 2025
- "Directors, Audit & Supervisory Board Members, and Executive Officers" and "Corporate Organization" updated.
- March 28, 2025
- "Directors, Audit & Supervisory Board Members, and Executive Officers" updated.
- January 6, 2025
- "Directors, Audit & Supervisory Board Members, and Executive Officers" updated.
MORE CONTENTS
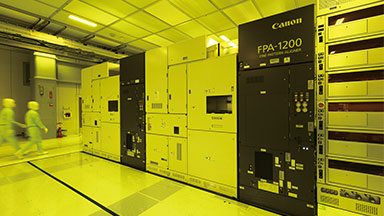
Nanoimprint Lithography
Nanoimprint Lithography "stamps" extremely fine patterns to form circuits.This video introduces the basic principles of the technology.
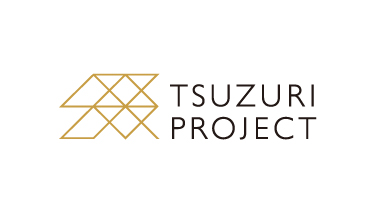
TSUZURI PROJECT
Preserving cultural assets for future generations and using these high resolution facsimiles for various purposes.
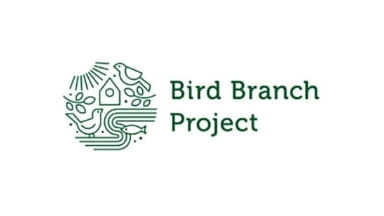
BIRD BRANCH PROJECT
The project highlights the cycle of life through various activities focusing on wild birds.
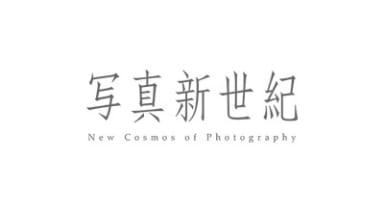
New Cosmos of Photography
The New Cosmos of Photography's archive site for a photography contest to discover, nurture and support new photographers.
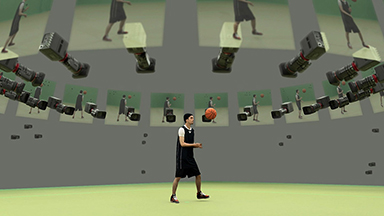
Volumetric Video Technology
Volumetric video is a technology which reconstructs a 3D space data from captured images. This video introduces the basic principles of the technology.
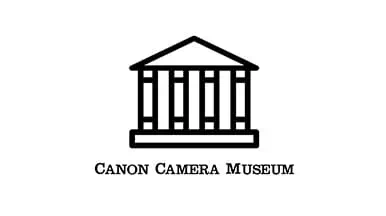
Canon Camera Museum
Canon Camera Museum provides historical information, such as the history of Canon and descriptions about all cameras and lenses released since it was founded.
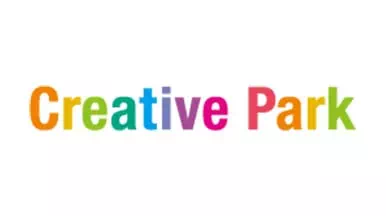
Canon Creative Park
You can download fashionable cards and fun paper craft for free. Enjoy everything right away with an inkjet printer and paper.
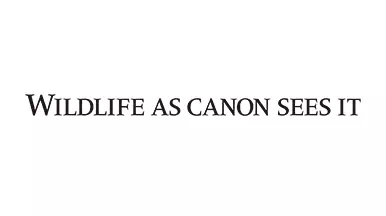
WILDLIFE AS CANON SEES IT
You can find advertisements featured in National Geographic until 2020.